How to Make Diesel Fuel from Used Motor Oil?
Used motor oil is a major waste product, generated in large quantities by the automotive and industrial sectors. It is estimated that over 25 billion gallons of used motor oil are generated worldwide each year. Of this, only about 60% is properly recycled or disposed of. The rest is often dumped illegally, which can pollute the environment.
Making used motor oil to diesel fuel is a good way to reduce the environmental impact. This can be done through a process called pyrolysis. Pyrolysis is a thermal decomposition process that breaks down organic matter in the absence of oxygen. When used motor oil is pyrolyzed, it is converted into a variety of products, including diesel fuel.
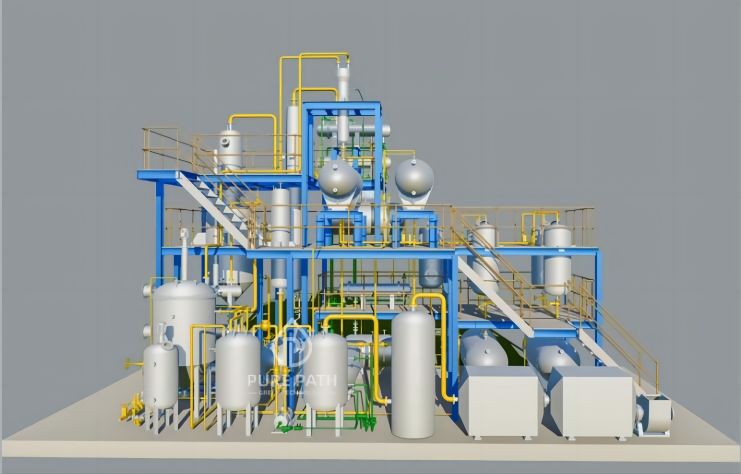
Producing diesel fuel from used motor oil has a number of benefits. It reduces the amount of waste that needs to be disposed of, and it helps to conserve fossil fuels. It also produces a fuel that is cleaner and more environmentally friendly than traditional diesel fuel.
Understanding What is Pyrolysis Process
The pyrolysis process can be carried out in a variety of ways. One common method is to use a batch reactor. In a batch reactor, the used motor oil is heated to a high temperature, typically in the range of 400-600 degrees Celsius. The oil is held at this temperature for a period of time, typically 1-2 hours. During this time, the oil breaks down into a variety of products, including diesel fuel.
After the pyrolysis process is complete, the products are cooled and condensed. The diesel fuel can then be separated from the other products using a variety of methods, such as distillation or centrifugation.
What Kind of Equipment Are Required in the Pyrolysis Process?
To produce diesel fuel from used motor oil, you will need the following equipment:
- A pyrolysis reactor
- A condenser
- A separator
- A safety system
The pyrolysis reactor is the vessel in which the used motor oil is heated and decomposed. The condenser cools the products of the pyrolysis process and causes them to condense into liquids. The separator separates the diesel fuel from the other products of the pyrolysis process.
The safety system is essential for preventing accidents. It should include a temperature sensor, a pressure sensor, and a gas detection system.
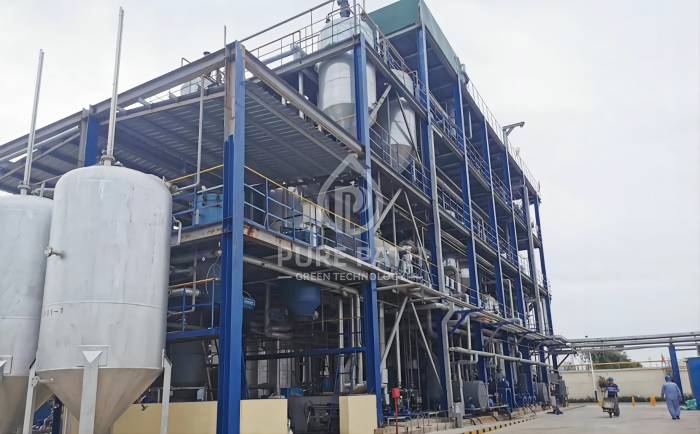
Process Steps of Pyrolysis
The following steps are involved in producing diesel fuel from used motor oil using a batch reactor:
- Prepare the used motor oil. The used motor oil should be filtered to remove any impurities. It is also important to remove any water from the oil, as water can cause the oil to foam and make it difficult to control the pyrolysis process.
- Load the used motor oil into the reactor. Fill the reactor with the used motor oil, leaving about 10% of the reactor empty to allow for expansion.
- Seal the reactor and start the heating process. Heat the reactor to the desired pyrolysis temperature, typically in the range of 400-600 degrees Celsius.
- Maintain the pyrolysis temperature for the desired period of time. The pyrolysis time will vary depending on the type of used motor oil and the desired yield of diesel fuel.
- Cool the reactor and condense the products. Once the pyrolysis process is complete, cool the reactor and condense the products using the condenser.
- Separate the diesel fuel from the other products. Use the separator to separate the diesel fuel from the other products of the pyrolysis process.
What Safety Precautions Should be Taken?
It is important to take safety precautions when producing diesel fuel from used motor oil. The pyrolysis process can be dangerous if not done properly.
The following safety precautions should be taken:
- Always wear personal protective equipment (PPE) when working with used motor oil and pyrolysis products. PPE includes gloves, goggles, a respirator, and a fireproof apron.
- Work in a well-ventilated area. Pyrolysis products can be flammable and toxic.
- Never leave the pyrolysis reactor unattended. The pyrolysis process can be unpredictable, and it is important to be able to respond quickly to any problems that may occur.
- Have a fire extinguisher on hand in case of a fire.
How is Product Yield?
The yield of diesel fuel from used motor oil will vary depending on the type of used motor oil and the pyrolysis conditions. However, in general, the yield of diesel fuel is typically in the range of 50-70% of the weight of the used motor oil.
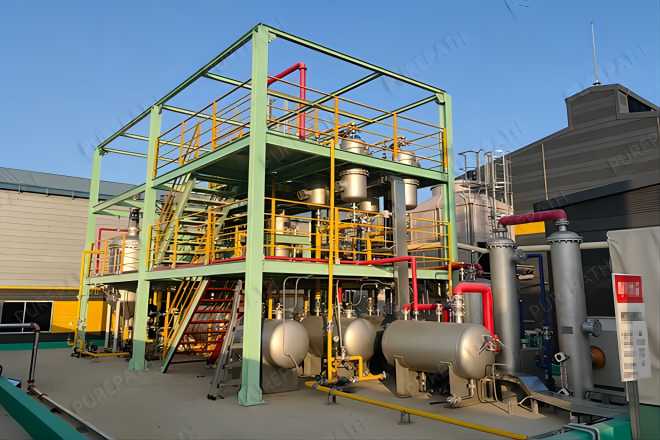
Conclusion
Producing diesel fuel from used motor oil is a viable way to reduce the environmental impact of used motor oil and to conserve fossil fuels. The pyrolysis process can be carried out in a variety of ways, but batch reactors are a common method. It is important to take safety precautions when producing diesel fuel from used motor oil, as the pyrolysis process can be dangerous if not done properly.
If you are curious about more process details of making used motor oil to diesel, Purepath is a professional manufacturer of used oil recycling plants in China, that can answer you professionally.