Something You Need to Know about Hydro-Cavitation Desulfurization Plant
In the pursuit of a cleaner and more sustainable future, technological advancements play a pivotal role. One such innovation that has gained significant attention in recent years is hydro-cavitation desulfurization. As global concerns over environmental pollution and health hazards escalate, the need to reduce harmful emissions from industrial processes, particularly sulfur emissions from fuels, has become paramount. Hydro-cavitation desulfurization has emerged as a promising solution, harnessing the power of cavitation to effectively mitigate sulfur content in fuels, contributing to cleaner energy production and a healthier planet.
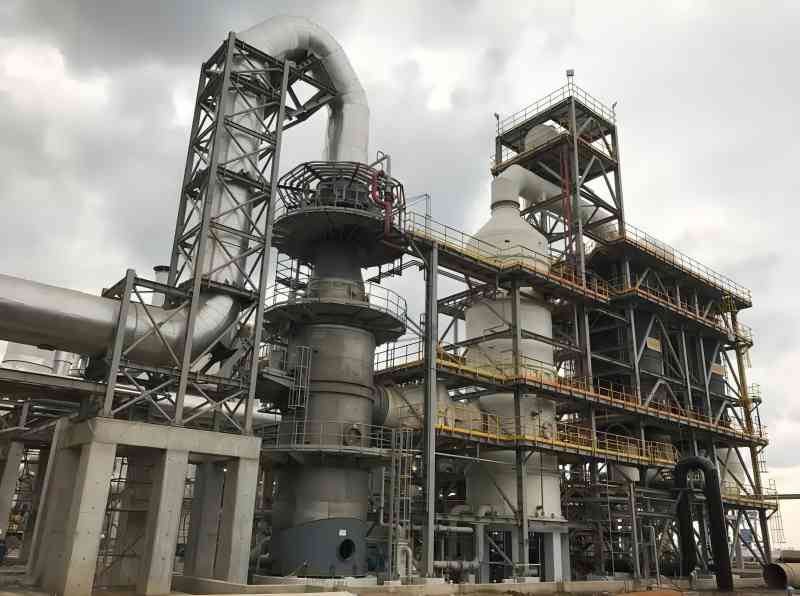
Introduction to Hydro-Cavitation Desulfurization
Desulfurization, the removal of sulfur compounds from fuels, is a critical process in reducing harmful emissions that contribute to air pollution and environmental degradation. Traditional methods of desulfurization involve complex chemical reactions or physical absorption processes. However, these methods often come with their own set of challenges, such as high energy consumption and the generation of secondary waste.
Hydro-cavitation desulfurization offers an innovative approach to this problem. It harnesses the power of cavitation, a phenomenon in which rapid changes in pressure lead to the formation, growth, and implosion of microscopic bubbles in a liquid. This implosion generates shock waves and intense local heat, creating conditions conducive to chemical reactions. When applied to desulfurization, hydro-cavitation proves to be remarkably effective.
Basic Principles of Hydro-Cavitation
At the heart of hydro-cavitation desulfurization lies the cavitation phenomenon. When a liquid experiences a sudden pressure drop, such as when it passes through a constriction, small vapor-filled cavities, or bubbles, form. These bubbles then collapse violently upon themselves due to the increased pressure, generating localized heat and pressure waves. This controlled chaos is what enables hydro-cavitation to facilitate chemical reactions that are otherwise challenging to induce.
In a hydro-cavitation desulfurization plant, the process begins with the intake of the fuel to be treated. This fuel is then subjected to the cavitation chamber, where it encounters rapid pressure changes that trigger cavitation. The cavitation bubbles create localized “hot spots” where sulfur compounds undergo chemical transformations, breaking down into less harmful substances. The result is a desulfurized fuel that meets stringent environmental regulations.
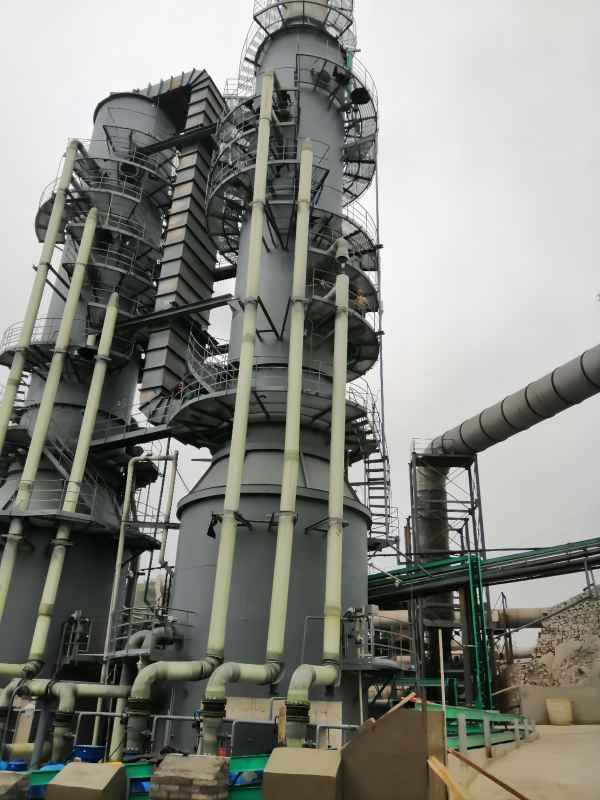
Components and Working of a Hydro-Cavitation Desulfurization Plant
A typical hydro-cavitation desulfurization plant consists of several essential components that work harmoniously to achieve efficient sulfur removal. These components include a reaction vessel or chamber, a cavitation generator, a sulfur separation unit, and sophisticated process controls and monitoring systems.
The desulfurization process begins with the intake of the fuel, which is subjected to pre-treatment to ensure its compatibility with the cavitation process. The fuel is then introduced into the cavitation chamber, where the pressure drop triggers the formation of cavitation bubbles. As these bubbles implode, the shockwaves created facilitate the breakdown of sulfur compounds, rendering them more susceptible to separation.
Following the cavitation stage, the mixture undergoes further processing to separate the desulfurized fuel from the sulfur compounds. Advanced separation techniques, such as centrifugation or filtration, are employed to achieve this goal. The desulfurized fuel can then be refined for optimal quality and performance.
Advantages of Hydro-Cavitation Desulfurization
The advantages of hydro-cavitation desulfurization are manifold and position it as a promising solution for the energy industry’s sustainability goals:
- High Efficiency in Sulfur Removal: Hydro-cavitation’s unique approach accelerates chemical reactions, resulting in a higher degree of sulfur removal compared to traditional methods. This efficiency contributes to cleaner fuel production and reduced emissions.
- Minimal Energy Consumption: Unlike some energy-intensive desulfurization methods, hydro-cavitation minimizes energy consumption, making it a more sustainable choice for industries striving to reduce their carbon footprint.
- Reduced Environmental Impact: Sulfur emissions are a major contributor to air pollution and acid rain, with detrimental effects on ecosystems and human health. Hydro-cavitation aids in significantly reducing these emissions, fostering a healthier environment.
- Versatility in Fuel Treatment: Hydro-cavitation is not limited to specific fuel types, making it suitable for a wide range of applications, from gasoline and diesel to alternative fuels like biodiesel and bioethanol.
- Potential for Co-Benefits: Apart from sulfur removal, hydro-cavitation can potentially enhance combustion efficiency and reduce other pollutant emissions, offering additional benefits beyond desulfurization.
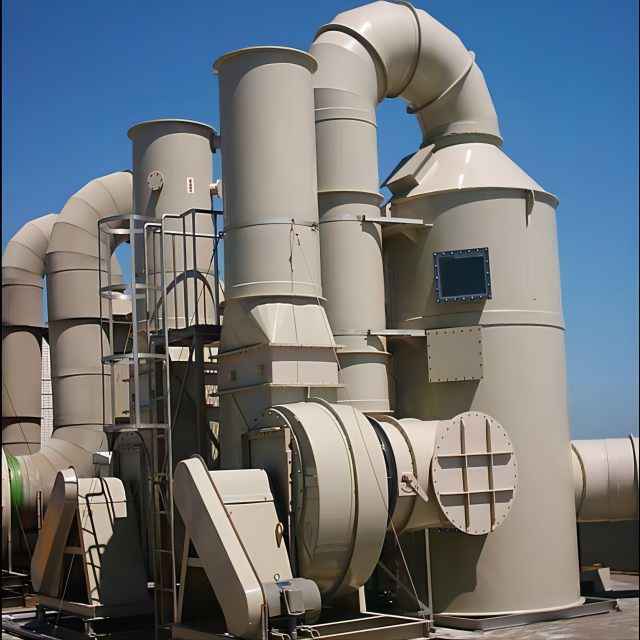
Conclusion
Hydro-cavitation desulfurization represents a groundbreaking advancement in the realm of clean energy production. By harnessing the power of cavitation, this method offers efficient sulfur removal while minimizing energy consumption and environmental impact. As the world shifts toward a more sustainable future, hydro-cavitation technology stands as a beacon of hope, driving us closer to a cleaner and healthier planet.