The Fundamentals of Mineral Base Oil Manufacturing Process
Roughly 95% of the current lubricant market is dominated by conventional (mineral-based) oils. While many are aware that these mineral oils originate from crude stocks, the intricacies of the refining process remain relatively unknown.
Mineral base oils, also known as conventional oils, form the backbone of the majority of lubricants used today. These oils are derived from crude oil and undergo a complex refining process to transform them into high-quality base stocks for various applications, from engine oil to hydraulic fluids.
Crude oil extracted from wells encompasses a diverse spectrum, ranging from light-colored oils comprising predominantly small hydrocarbon molecular chains to dense, almost solid asphalt-like compounds with large hydrocarbon chains.
These crude oils present highly complex mixtures containing an array of diverse compounds composed of hydrogen and carbon. Referred to as hydrocarbons, these compounds vary in size, ranging from methane with one carbon and four hydrogen atoms to sprawling structures containing 60 or more carbon atoms. Leveraging this distribution in molecular size can prove advantageous in refining processes.
The Importance of Base Oil Refinery
Base oil refineries play an undeniably critical role in our modern world. They serve as the bridge between the naturally occurring resource, crude oil, and the essential lubricants that keep our machinery functioning smoothly. These lubricants play a vital role in reducing friction, wear, and heat, ultimately ensuring the efficient operation of various machines across diverse industries.
1. The Lubrication Lifeline
Without the vital products of base oil refineries, our transportation systems would face significant challenges. Engine oil, a crucial lubricant derived from base oil, minimizes friction between moving parts within an engine, preventing excessive wear and tear. This ensures the smooth and efficient operation of vehicles, allowing us to commute, transport goods, and maintain crucial services like emergency response and public transportation.
2. Beyond Transportation
The impact of base oil refineries extends far beyond the realm of transportation. Industrial machinery, a cornerstone of various industries like manufacturing and construction, relies heavily on lubricants derived from base oil. These lubricants act as a protective layer, minimizing friction and wear on critical components, thereby ensuring the smooth operation of production lines, construction equipment, and other industrial machinery.
3. Everyday Applications
The reach of base oil refineries extends even further, touching upon our daily lives in ways we might not readily recognize. The lubricants used in household appliances like refrigerators, air conditioners, and even washing machines often have base oil as a key component. These lubricants ensure the smooth operation of these appliances, contributing to their longevity and efficient performance.
4. The Bottom Line
In conclusion, base oil refineries serve as an essential cog in the machinery of our modern world. By transforming crude oil into high-quality base stocks, they enable the production of lubricants that are critical for the efficient operation of a vast array of machines, from automobiles and industrial equipment to everyday household appliances. Their role, though often unseen, is undeniably crucial in ensuring the smooth functioning of our society.
Two Base Oil Manufacturing Process
Extraction Process

1. Deasphalting:
Propane deasphalting is a crucial step in the refining process, particularly for heavy crude oil fractions. This process targets the residuum found at the bottom of the distillation column, which comprises the heaviest and largest molecules. By subjecting this residue to propane deasphalting, the molecules are separated into two distinct products: tar and deasphalted oil.
Deasphalted oil, the primary output of this process, shares similarities with lube distillates but boasts a higher boiling point. It undergoes further refinement through processes akin to those applied to lube distillates. This refined deasphalted oil serves as a valuable base stock for various applications, including lubricants and other petroleum products.
2. Solvent Extraction:
Solvent extraction plays a pivotal role in refining oil distillates, primarily aimed at removing aromatics and other undesirable constituents. This process employs solvents like phenol, furfural, and sulfur dioxide to extract these unwanted components effectively.
Upon solvent extraction, two main products emerge: raffinates, often referred to as neutral oils, and an extract enriched with aromatic content. The raffinates serve as base stocks for lubricants, while the aromatic-rich extract finds utility as a process oil or fuel oil due to its unique properties.
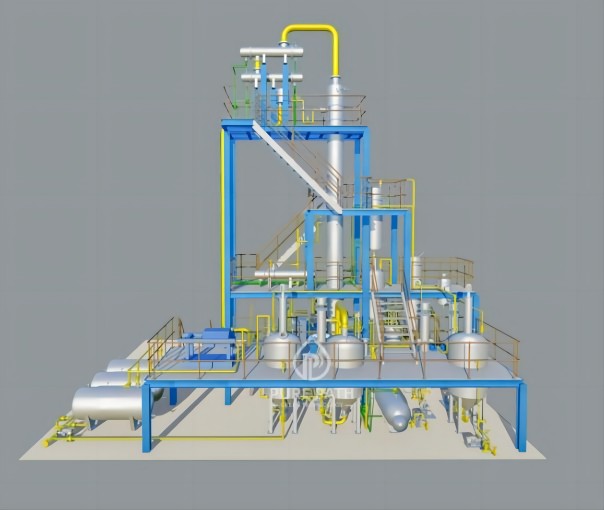
3. Dewaxing:
Following solvent extraction, dewaxing is employed to enhance the low-temperature fluidity of the refined oils. This process results in the production of two distinct products: a byproduct wax characterized by its predominantly paraffinic composition, and a dewaxed oil containing paraffins, naphthenes, and some aromatics.
The dewaxed oil serves as a crucial base stock for many lubricants. However, to elevate it to a premium product, an additional refining step is often undertaken.
4. Hydrofinishing:
Hydrofinishing represents the final refinement stage for base oils, refining them to achieve superior quality. This process involves a chemical reaction with hydrogen, targeting polar compounds present in the oil.
Through hydrofinishing, the oil undergoes a transformation, resulting in a lighter-colored product with improved chemical stability. The effectiveness and quality of the base oil produced depend on the severity of the temperature and pressure conditions applied during the hydrofining process.
Conversion Process

1. Hydrocracking
Hydrocracking is a sophisticated refining process crucial for transforming heavy hydrocarbon fractions into lighter, more valuable products such as gasoline, diesel, and jet fuel. This process involves subjecting the distillates to a chemical reaction with hydrogen in the presence of a catalyst, typically at high temperatures (around 420 degrees Celsius) and pressures (approximately 3,000 pounds per square inch or psi).
During hydrocracking, the complex hydrocarbon molecules present in the feedstock undergo significant structural alterations. Aromatic and naphthene rings, characteristic of heavier hydrocarbons, are broken and opened. These broken bonds are then restructured and joined with hydrogen atoms to form shorter, branched-chain hydrocarbons known as isoparaffins.
The use of hydrogen in hydrocracking serves multiple purposes. Firstly, it facilitates the fragmentation of complex hydrocarbon molecules, enabling the conversion of heavy feedstocks into lighter, more valuable products. Additionally, hydrogenation reactions aid in saturating unsaturated hydrocarbons, thereby increasing the stability and quality of the final products. Furthermore, hydrogen serves as a vital agent for removing impurities such as water, ammonia, and hydrogen sulfide from the feedstock, thereby enhancing the purity and value of the resulting hydrocarbon products.
2. Hydrodewaxing
Hydrodewaxing, similar to hydrocracking, is a hydrogenation process employed to modify the properties of petroleum feedstocks. Specifically, hydrodewaxing targets the removal of waxy normal paraffins, which contribute to high viscosity and poor cold-flow properties in finished products such as diesel and lubricating oils. Like hydrocracking, hydrodewaxing utilizes a hydrogenation unit equipped with a specific catalyst tailored to promote the conversion of waxy normal paraffins into more desirable isoparaffin structures. This conversion leads to the production of lighter, low-viscosity hydrocarbons with improved cold-flow characteristics, enhancing the performance and usability of the final products.
3. Hydrotreating
Hydrotreating is a fundamental process often employed in conjunction with hydrocracking and hydrodewaxing to further refine petroleum feedstocks and improve product quality. Since hydrocracking and hydrodewaxing involve the breaking of chemical bonds between carbon atoms, unsaturated hydrocarbons may be formed as intermediate or byproducts. Hydrotreating addresses this issue by introducing additional hydrogen into the system, saturating any unsaturated molecules present in the feedstock. The resulting saturated hydrocarbons exhibit enhanced stability and resistance to oxidation, thereby improving the overall quality and longevity of the final products. Additionally, hydrotreating serves to remove sulfur, nitrogen, and other impurities, ensuring compliance with stringent environmental regulations and enhancing the marketability of the refined products.
Mineral Base Oils
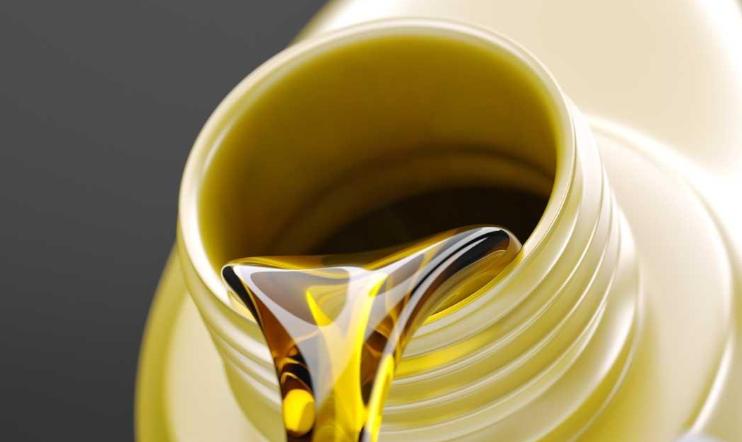
The base oil is the foundation of a finished lubricant. A finished lubricant is one that is ready for use and is a blend of both base oil(s) and additives. Remember, the additives formulated into the mineral base oil will alter the properties of the base oil.
The basic function of a refinery is to separate the crude oil into its useful components and remove the components of unwanted materials. Base oils or base stocks, as they are sometimes called, are created from separating and cleaning up crude oil. They are one of several liquid components that are created from crude oil.
Gasoline is the lightest or smallest hydrocarbon component, followed by kerosene or jet fuel, diesel fuel, base oils, waxes, and asphalt or bitumen, which is the heaviest, thickest material. Base oils are prepared from crude oils through the use of the following series of processes which, to some degree, must be applied to all crude oils for refining and also re-refining processes.
Base Oil Refining Process
Base oils serve as the foundation for lubricating oils, and they are typically created in four different viscosity grades within the refinery distillation process. These grades enable the production of various ISO and API viscosity grades, catering to a wide range of lubrication applications.
1. Atmospheric Distillation: This is the initial step in the refinery distillation process, primarily aimed at separating lighter hydrocarbons, such as gasoline and diesel, from the rest of the crude petroleum. Distillation, a separation process, yields products known as distillates.
2. Vacuum Distillation: This process is employed to distill and separate heavier fractions that would not efficiently distill at atmospheric pressure without risking damage. Vacuum distillation is crucial for obtaining the initial base oil viscosity and flash point characteristics. It provides four distinct viscosity fractions (or distillates), which serve as the starting materials for the production of finished oil products.
3. Refining: The refining process is pivotal for enhancing the quality and performance of base oils. It involves the removal of unwanted chemical structures, such as aromatic rings, to reduce the base oil’s susceptibility to aging in service and to improve its viscosity-temperature characteristics. Oil companies utilize three basic refining processes:
- Sulphuric acid/clay refining: An outdated method that involves the use of sulphuric acid and clay for purification.
- Solvent extraction: Commonly used in mid-20th-century refineries, this process utilizes solvents to extract impurities from the base oil.
- Catalytic hydrogenation or hydrotreating: Introduced in the 1980s, this modern process involves the use of hydrogen and catalysts to remove impurities and improve the quality of the base oil.
4. De-asphalting: This step in the refining process focuses on removing heavy asphalt residue from the valuable distillate fractions, ensuring the purity and quality of the base oil.
5. De-waxing: De-waxing is essential for reducing the wax content of the base oil, thereby enhancing its low-temperature properties. This process ensures that the lubricating oil remains effective even in cold environments.
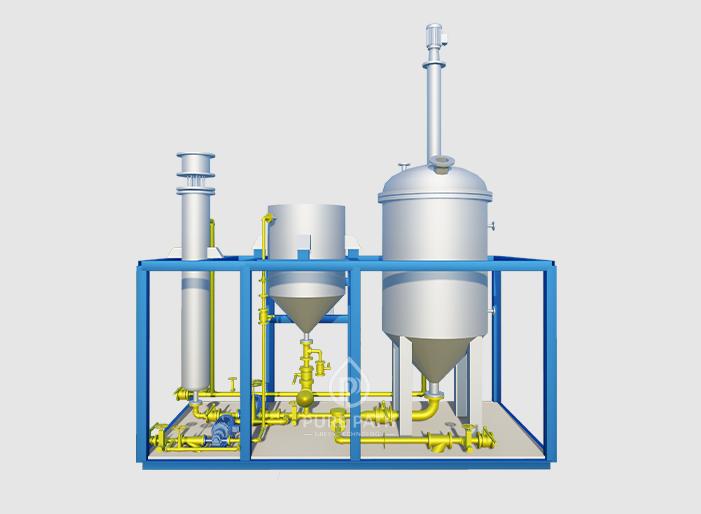
6. Blending: The final stage in producing finished lubricating oil involves blending different base oils to achieve the desired viscosity. Additionally, specified additives are incorporated to impart specific properties to the finished oil, ensuring optimal lubricating performance in various applications. Blending is a crucial step that enables the customization of lubricating oils to meet the specific requirements of different industries and machinery.