How Waste Oil to Diesel Machine Work?
In today’s world, reducing our environmental impact and finding alternative fuel sources are critical concerns. Waste oil, a byproduct of various industrial processes and vehicle use, poses a significant environmental threat if not disposed of properly. Waste oil to diesel machines offer a solution by transforming this waste into a usable fuel source, diesel. This article delves into the inner workings of these machines, exploring the process, benefits, and considerations surrounding this innovative technology.

The Transformation Process: From Used Engine Oil to Diesel Fuel
Waste oil to diesel machines rely on a multi-stage process to transform used engine oil into a usable fuel. While some machines might involve an initial cleaning step, the core functionality centers around distillation. Distillation is a technique used to separate components within a liquid mixture based on their boiling points. Here’s a detailed breakdown of each step:
1. Pre-processing
This initial stage depends on the specific machine and the condition of the used oil. If necessary, pre-processing involves removing large contaminants like dirt, metal shavings, or water. This is typically achieved through filtration systems. Pre-processing ensures a smoother distillation process by minimizing any disruptions caused by these contaminants and protects the machine’s internal components from potential damage.
2. Distillation
This is the central step in making diesel from used motor oil. Here’s a closer look:
- Heating the Used Engine Oil: To initiate the process, the used oil needs to reach a high temperature. Waste oil to diesel machines utilize indirect heating systems for safety reasons. These systems transfer heat from an external source, such as a furnace or boiler, to the oil container through a heat exchanger. This heat exchanger acts as a barrier, preventing open flames from directly contacting the oil, significantly reducing the risk of fire or explosions.
- Conversion to Gas and Separation: As the temperature increases within the oil container, the various components in the used oil begin to vaporize at different rates. Lighter hydrocarbon molecules, which are the fundamental building blocks of diesel fuel, have lower boiling points and turn into gas first. These lighter gas fractions are then separated from the heavier components that remain in a liquid state at the bottom of the distillation chamber.
- Cooling and Condensation: Once separated, the gaseous hydrocarbons are directed through a dedicated cooling system. Here, their temperature is drastically lowered, causing them to change back into a liquid state through condensation. This condensed liquid is the newly created diesel fuel. The efficiency of the cooling system plays a critical role in maximizing the amount of diesel fuel obtained from the used oil.
3. Purification
Some waste oil to diesel machines might include an additional purification stage. This stage involves treating the newly created diesel fuel with chemical solutions or filtration systems. The purpose is to remove any remaining impurities, color, or odor from the fuel. This additional step enhances the quality of the produced diesel, making it more comparable to commercially available diesel fuel in terms of cleanliness.
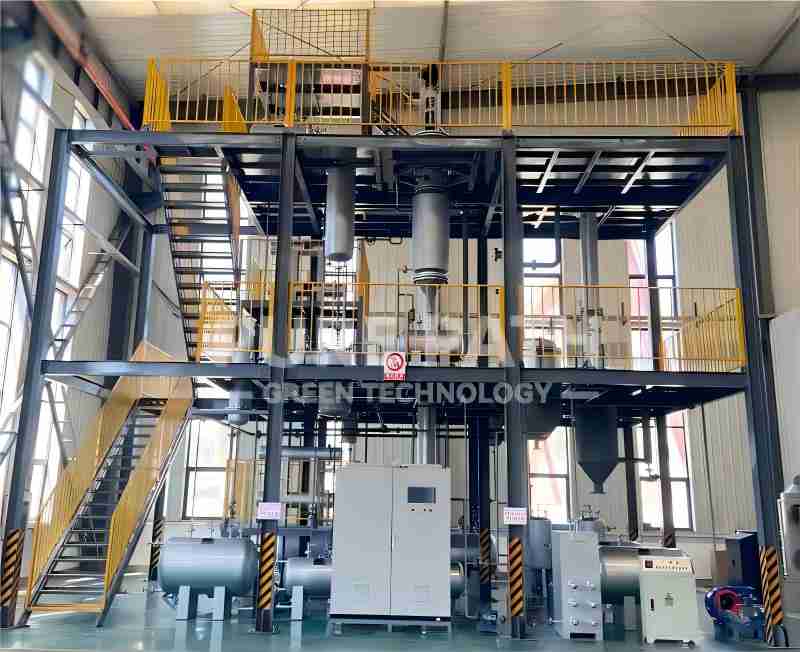
Benefits of Utilizing Waste Oil to Diesel Machines
The benefits of employing waste oil to diesel machines are multifaceted, encompassing both environmental and economic advantages.
- Environmental Benefits: Improper disposal of used oil can have devastating consequences for the environment. It can contaminate soil and water sources, harming plant and animal life. Waste oil to diesel machines offer a sustainable solution by transforming this waste into a usable fuel source. This not only reduces the environmental impact of used oil disposal but also promotes resource conservation. By recycling used oil, we lessen our dependence on virgin crude oil, a non-renewable resource.
- Economic Benefits: The rising cost of conventional diesel fuel can be a significant burden for businesses and individuals who rely on diesel-powered equipment. Waste oil to diesel machines offer a potential cost-saving solution. By converting used oil into a usable fuel source, users can potentially reduce their dependence on commercially purchased diesel, leading to lower fuel expenses.
Considerations When Using Waste Oil to Diesel Machines
While waste oil to diesel machines offer numerous advantages, there are some important considerations to keep in mind:
- Regulations: Government regulations regarding the processing and use of waste oil vary by location. It’s crucial to research and comply with all local and federal regulations before operating a waste oil to diesel machine. Additionally, the quality of the produced diesel fuel might not always meet the exact standards of commercially available diesel. In some cases, the resulting fuel might require blending with commercially refined diesel to ensure compatibility with specific engines.
- Safety Precautions: Waste oil to diesel machines involve high temperatures and flammable materials. Therefore, adhering to strict safety protocols is essential. This includes using appropriate personal protective equipment (PPE), having a fire extinguisher readily available, and ensuring proper ventilation in the operating area. It’s also crucial to follow the manufacturer’s instructions for safe operation and maintenance of the machine.
- Quality of Produced Diesel Fuel: The quality of the produced diesel fuel can be influenced by several factors, including the type and condition of the used oil being processed, the efficiency of the machine, and the presence of any additional purification steps. While the resulting fuel can be suitable for powering various diesel-powered equipment, it may not always be identical to commercially available diesel in terms of properties like cetane rating (a measure of ignition quality). Consulting with a qualified professional or machine manufacturer is recommended to determine the specific characteristics of the produced fuel and its compatibility with different engine types. In some instances, blending the homemade diesel with commercially refined diesel can be necessary to ensure optimal engine performance and emissions control.
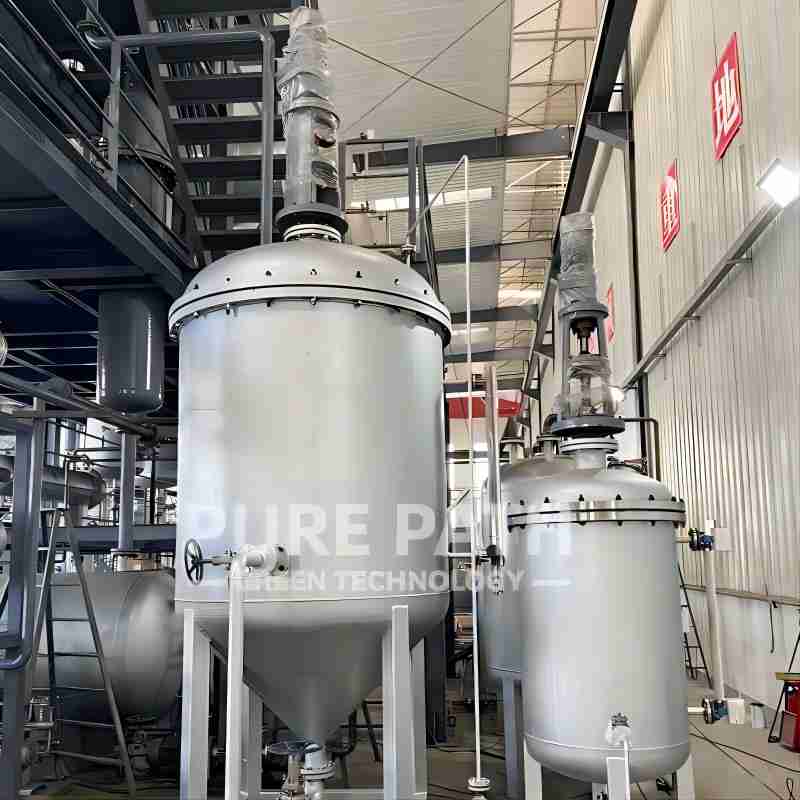
What Else Can Be Improved in Waste Oil to Diesel Technology?
Waste oil to diesel machines offer a promising solution for managing waste and conserving resources. As research and development efforts continue, we can expect advancements that significantly improve the efficiency and effectiveness of these machines. Here’s a closer look at some key areas with the potential for future improvements:
1. Enhanced Processing Techniques
- Higher Yield Extraction: Current technology can be further refined to extract a greater percentage of usable fuel from the waste oil. This can be achieved through improvements in distillation methods, potentially involving the exploration of techniques like vacuum distillation or the use of catalysts to break down heavier hydrocarbon molecules into lighter ones suitable for diesel fuel.
- Reduced Energy Consumption: Optimizing the heating process within the machine is crucial. This might involve developing more efficient heat exchangers or exploring alternative heating methods that minimize energy use during the distillation process.
2. Advanced Purification Methods
- Improved Fuel Quality: Current purification methods can be further enhanced to create diesel fuel with properties that more closely match commercially available diesel. This could involve the development of more sophisticated filtration systems or the incorporation of chemical treatments that remove impurities to a greater degree. The goal would be to eliminate the need for blending homemade diesel with commercially refined diesel altogether.
3. Automation and Control System Integration
- Optimized Distillation Process: Implementing advanced automation and control systems can significantly improve the overall efficiency of the distillation process. These systems can precisely monitor and adjust factors like temperature, pressure, and flow rates within the machine. This level of control can ensure consistent fuel quality and optimize the yield of usable diesel fuel.
- Enhanced Machine Safety: Advanced control systems can also play a crucial role in maximizing machine safety. Real-time monitoring of critical parameters can help prevent potential malfunctions or accidents by automatically triggering safety protocols if necessary.
By addressing these areas for improvement, waste oil to diesel machines have the potential to become even more attractive solutions. This technology can benefit businesses and individuals seeking to reduce their environmental impact by minimizing waste oil disposal and potentially lowering fuel costs through the use of a converted fuel source.
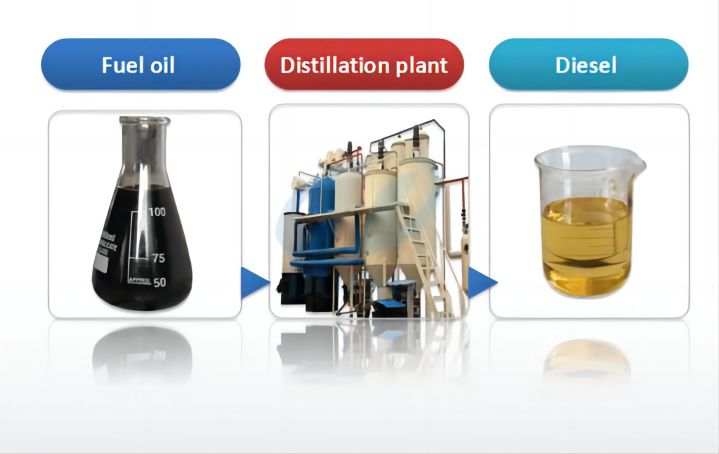
Conclusion
Waste oil to diesel machines offer a compelling solution for transforming a potential environmental hazard into a valuable resource. By utilizing distillation processes, these machines convert used oil into a usable fuel source, promoting sustainability and resource conservation. While considerations regarding regulations, safety, and fuel quality exist, ongoing advancements in technology promise to further refine this process. As waste oil to diesel technology continues to evolve, it has the potential to play a significant role in creating a cleaner and more sustainable future.