Solvent Extraction Plant: A Modern Solution for Waste Oil Refinery
Lubricants play a vital role in modern machinery, reducing friction and wear to ensure smooth operation. Base oils are the primary component of lubricants, and their quality directly affects the performance and lifespan of these lubricants. Traditionally, base oils have been derived from crude oil through a complex refining process. However, with increasing environmental concerns and a growing demand for sustainable practices, alternative methods for obtaining high-quality base oils are gaining traction.
Solvent extraction plants have emerged as a significant technology in this regard. These industrial facilities utilize a specialized process to refine and enhance the characteristics of base oils.
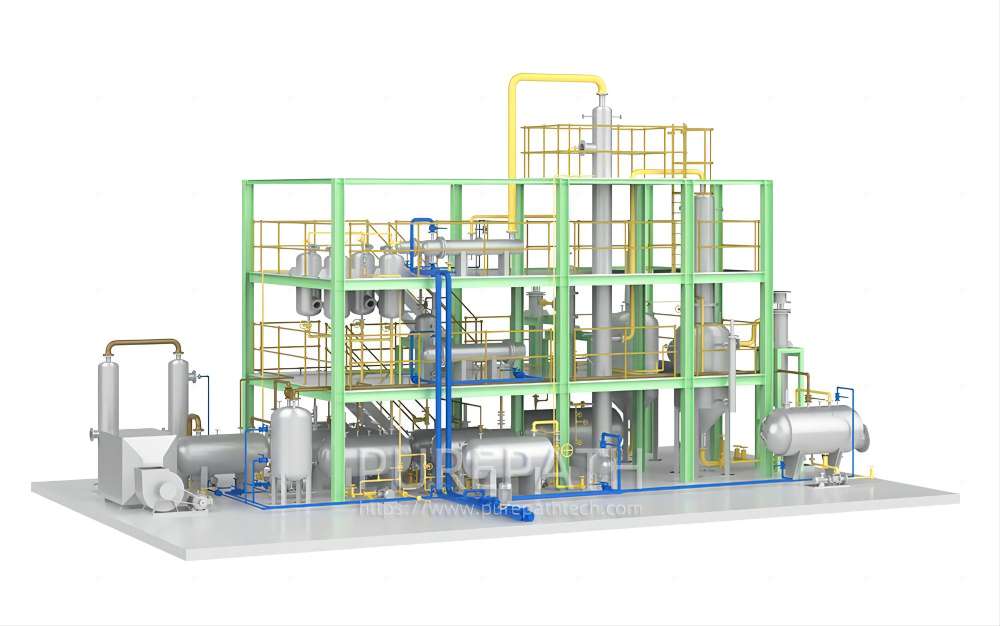
Waste Oil Refinery and Challenges: Environmental and Technical Concerns
Waste oil, also known as used oil, is any lubricating oil that has become unusable for its original purpose due to contamination. This contamination occurs during the oil’s service life through exposure to heat, friction, and combustion byproducts. Common sources of waste oil include:
- Motor vehicles: Engine oil used in cars, trucks, motorcycles, and other motorized vehicles.
- Industrial machinery: Lubricating oil used in manufacturing equipment, machine tools, and industrial processes.
- Hydraulic systems: Oil used to transmit power and control movement in hydraulic machinery like construction equipment and presses.
Improper disposal of waste oil poses a severe environmental threat. Here’s a breakdown of the dangers:
- Soil and water contamination: When improperly disposed of, waste oil can seep into the ground, contaminating soil and groundwater. This contamination can harm plant life and disrupt ecosystems. Oil can also migrate to surface water sources like rivers and lakes, impacting aquatic life and making the water unsuitable for human consumption or recreation.
- Air pollution: The improper burning of waste oil releases harmful pollutants into the atmosphere. These pollutants can include volatile organic compounds (VOCs), particulate matter (PM), and heavy metals. VOCs contribute to smog formation and respiratory problems, while PM can irritate the lungs and exacerbate asthma. Heavy metals, such as lead and cadmium, can accumulate in the environment and pose long-term health risks.
Traditional waste oil refining methods, specifically clay treatment, have limitations that hinder efficiency and quality:
- Limited contaminant removal: Clay treatment primarily targets specific impurities but struggles to remove a broader range of contaminants present in used oil. This results in a re-refined oil that may still contain undesirable components.
- Spent clay waste: The clay used in the process becomes saturated with contaminants and needs disposal. This generates additional waste that requires proper management, adding to the overall environmental impact.
- Subpar re-refined oil quality: The base oil obtained through clay treatment may not always meet the stringent specifications required for modern lubricants. These specifications involve properties like viscosity index, oxidation stability, and pour point, which are crucial for optimal lubricant performance.
These limitations highlight the need for more effective and environmentally friendly waste oil refinery methods, such as solvent extraction.
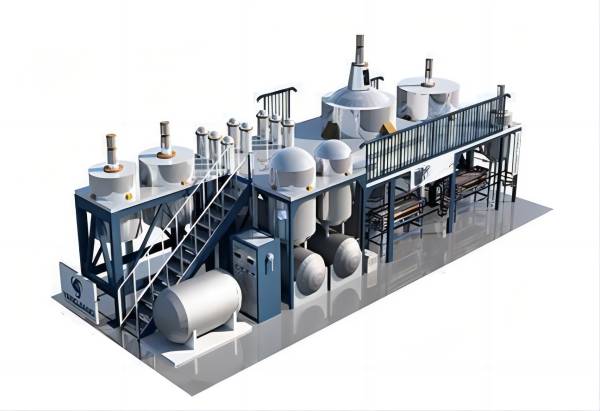
Solvent Extraction Plant for Waste Oil Re-refining
PurePath’s PPGT-BE base oil solvent extraction plant represents a significant advancement in waste oil refinery. This technology utilizes a multi-stage process designed to remove a broader spectrum of contaminants from used oil, resulting in a higher-quality base oil product. Here’s a breakdown of the solvent extraction process:
1. Mixing: The used oil is introduced into a mixing vessel. Here, it is combined with a specifically chosen solvent. This solvent is selected for its high affinity towards undesirable components present in the used oil. These undesirable components include:
- Polycyclic aromatic hydrocarbons (PAHs): These are carcinogenic compounds formed during the combustion process within engines.
- Gums: These are sticky, non-lubricating materials that can degrade oil performance over time.
- Asphaltenes: These are heavy, tar-like molecules that can thicken oil and contribute to sludge formation.
- Sulfur, nitrogen, and oxygen compounds: These elements can negatively impact the oxidation stability and anti-wear properties of lubricants.
2. Selective Dissolution: The solvent’s high affinity for these target contaminants causes them to selectively dissolve within the solvent, separating them from the desired base oil components. This separation occurs at a molecular level.
3. Solvent & Impurity Removal: Following the selective dissolution stage, the mixture progresses through a series of distillation and purification stages. These stages are designed to remove the used solvent and the dissolved impurities from the oil.
- Distillation typically involves applying heat and pressure to separate components based on their differing boiling points. The solvent, having a lower boiling point than the base oil, will vaporize first and can be collected for reuse in subsequent extraction cycles.
- Purification stages may employ additional techniques like filtration or adsorption to remove any remaining trace contaminants.
4. Clean and Improved Base Oil: The final product is a significantly cleaner base oil compared to the original used oil. This re-refined base oil possesses improved properties such as:
- Enhanced viscosity index: This translates to better performance across a wider range of operating temperatures.
- Increased oxidation stability: The re-refined oil exhibits a greater resistance to breakdown due to oxidation, extending its lifespan.
- Lower pour point: This allows the oil to flow more readily at lower temperatures, improving cold-start performance in machinery.
By removing these contaminants and enhancing the base oil’s properties, solvent extraction offers a superior alternative to traditional waste oil refining methods.
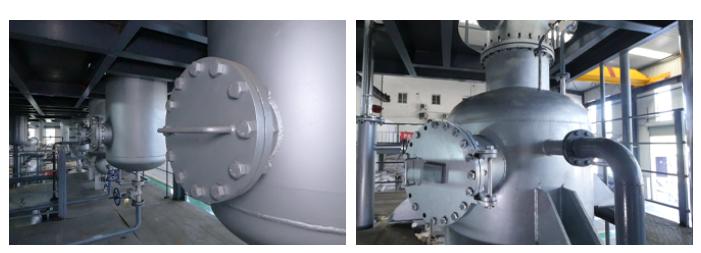
Benefits of Using Solvent Extraction
Compared to traditional clay treatment methods, solvent extraction offers several advantages in waste oil refinery:
- Improved Efficiency: Solvent extraction exhibits a higher removal rate for contaminants, resulting in a cleaner and purer base oil product. This translates to a more efficient use of waste oil as a source of base stock.
- Higher Quality Base Oil Output: The solvent extraction process removes a broader spectrum of impurities compared to clay treatment. This leads to a re-refined base oil with improved properties such as viscosity index, oxidation stability, and pour point. These enhanced characteristics enable the re-refined oil to meet the American Petroleum Institute (API) Group 1+ standards, making it suitable for various high-performance lubricant applications.
- Reduced Environmental Impact: Solvent extraction minimizes the environmental impact associated with waste oil disposal. By effectively converting used oil into high-quality base stock, this technology reduces the reliance on virgin crude oil for lubricant production. Additionally, the process generates less waste compared to clay treatment, as the solvent can be recycled and reused in subsequent extraction cycles.
- Economic Advantages: The utilization of waste oil as a source of base stock through solvent extraction offers economic benefits. It reduces the dependence on virgin crude oil, a finite resource with fluctuating prices. Furthermore, by providing a solution for waste oil disposal, solvent extraction helps businesses comply with environmental regulations and potentially avoid associated costs.
Applications of Re-refined Base Oil
The high-quality base oil produced through solvent extraction can be used in a wide range of lubricant applications, including:
- Engine Oils: Re-refined base oil can be used to formulate engine oils for various types of vehicles, including passenger cars, trucks, and heavy machinery. These re-refined engine oils offer comparable performance to lubricants made from virgin base stock.
- Industrial Lubricants: The improved properties of re-refined base oil make it suitable for formulating industrial lubricants used in machinery across diverse sectors like manufacturing, mining, and construction.
- Hydraulic Fluids: Solvent-extracted base oil can be used to create high-performance hydraulic fluids for industrial equipment and machinery requiring precise control and power transmission.
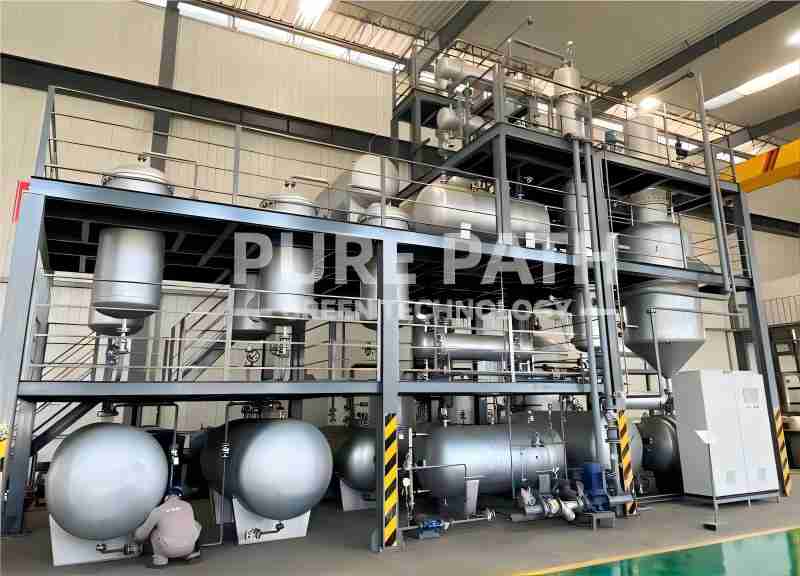
Conclusion
Solvent extraction plants represent a significant advancement in waste oil refinery. This technology provides an environmentally responsible solution for managing used oil while offering a high-quality, sustainable source of base oil for the lubricant industry. As environmental concerns and the demand for sustainable practices continue to grow, solvent extraction plants are poised to play an increasingly crucial role in the future of lubricant production. By promoting resource conservation, reducing environmental pollution, and offering a cost-effective alternative to virgin crude oil, solvent extraction technology paves the way for a more sustainable future for the lubricant industry.