The Life Cycle Challenge: Can Solvent Extraction Plants Become Truly Sustainable?
Oil solvent extraction plants play a vital role in our modern world, producing a wide range of products from cooking oils to biofuels. However, the traditional methods employed raise concerns about their environmental impact. This article delves into the life cycle of solvent extraction, analyzing its sustainability challenges and exploring potential solutions for a greener future.
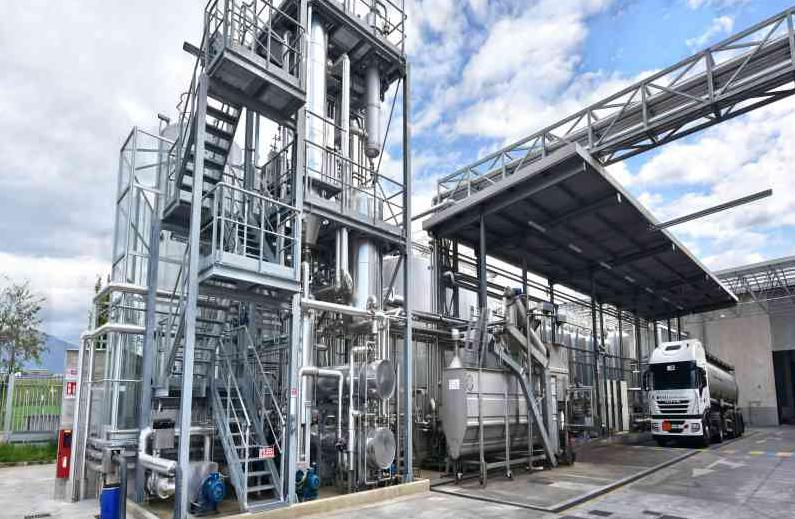
Understanding the Oil Solvent Extraction Process
Solvent extraction is a widely used industrial technique for separating desired components from a mixture. In the context of oil, it plays a crucial role in extracting valuable products like lubricants, fuels, and waxes from heavier crude oil. The process typically involves several stages, each of which is essential for efficient extraction and sustainability.
1. Preparation:
The crude oil undergoes pre-treatment to remove impurities and adjust its viscosity, ensuring optimal conditions for the extraction process. This step is crucial for maintaining the quality of the final products and preventing contamination.
2. Extraction:
Once prepared, the crude oil is mixed with a solvent chosen for its ability to selectively dissolve the desired components while leaving impurities behind. Common solvents used in oil extraction include n-hexane and propane. This selective dissolution process allows for the efficient separation of valuable products from the crude oil mixture.
3. Separation:
After extraction, the resulting oil-solvent mixture undergoes separation to isolate the target oil products from the solvent. Various techniques such as distillation or evaporation are employed to separate the components based on their boiling points or physical properties. This step is crucial for obtaining high-purity oil products and minimizing waste.
4. Solvent Recovery:
Ideally, the used solvent is recovered through processes like distillation and reused in the extraction cycle. Solvent recovery is essential for minimizing resource consumption, reducing costs, and mitigating environmental impacts. By recovering and reusing solvents, solvent extraction plants can significantly reduce their environmental footprint and enhance overall sustainability.
However, while solvent extraction offers numerous benefits, it also poses challenges in terms of environmental sustainability.
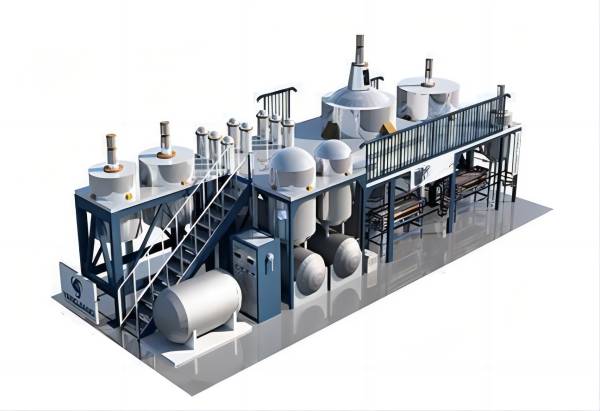
Environmental Concerns Throughout Oil Solvent Extraction Process
Navigating the complexities of environmental concerns throughout the oil solvent extraction process is crucial for fostering sustainable practices within the industry. Here are some key considerations:
- Volatile Organic Compound (VOC) Emissions: Hexane, a commonly used solvent in extraction, emits volatile organic compounds (VOCs) during the extraction process. These emissions pose health risks to workers and contribute to air pollution. Employing technologies such as closed-loop systems and effective ventilation can help mitigate these emissions, ensuring a safer working environment and reducing the plant’s environmental impact.
- Waste Management: The disposal of solvent-laden waste streams requires careful attention to prevent environmental contamination. Implementing efficient waste management practices, such as solvent recovery systems and proper containment measures, can minimize the risk of soil and water pollution. Additionally, exploring opportunities for waste stream reuse or recycling can further enhance sustainability efforts.
- Energy Consumption: The energy-intensive nature of solvent extraction processes contributes to greenhouse gas emissions and operational costs. Embracing energy-efficient technologies, optimizing process parameters, and incorporating renewable energy sources can reduce energy consumption and mitigate the plant’s carbon footprint. This not only benefits the environment but also enhances cost-effectiveness and long-term competitiveness.
- Water Usage: Water is essential for various aspects of solvent extraction, including equipment cleaning, cooling, and steam generation. However, excessive water consumption can strain local water resources and contribute to environmental degradation. Implementing water conservation measures, such as recycling wastewater and adopting water-efficient technologies, can help minimize the plant’s water footprint and ensure responsible resource management.
- Regulatory Compliance: Adhering to environmental regulations and standards is paramount for solvent extraction plants to operate sustainably. Regular monitoring, reporting, and compliance with air and water quality regulations are essential to prevent environmental harm and maintain public trust. Engaging with regulatory authorities, conducting environmental assessments, and investing in continuous improvement initiatives demonstrate a commitment to environmental responsibility.
By addressing these environmental concerns proactively and incorporating sustainable practices into every stage of the oil solvent extraction process, plants can enhance their environmental performance and contribute to a more sustainable future. Collaborating with industry peers, leveraging innovative technologies, and fostering a culture of environmental stewardship is key to overcoming challenges and achieving long-term sustainability goals.
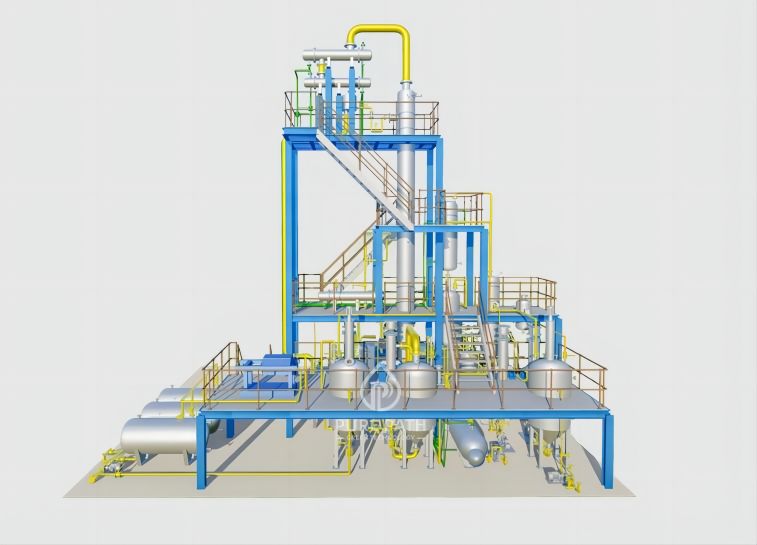
Assessing Sustainability Across the Oil Solvent Extraction Life Cycle
Achieving true sustainability for solvent extraction plants requires a comprehensive strategy that tackles environmental concerns across the entire life cycle, from cradle to grave. Here’s a deeper dive into key areas for improvement:
1. Input Materials:
- Solvent Selection: Moving away from traditional petroleum-derived solvents is critical. Bio-based alternatives like vegetable oils or even CO2 offer a more sustainable option. These solvents are often less volatile, reducing air emissions, and some can even be derived from renewable sources.
- Life Cycle Assessment of Solvents: Conducting LCAs on potential new solvents helps understand their overall environmental impact, including their production, transportation, and potential for end-of-life recycling or disposal.
2. Process Optimization:
- Closed-Loop Solvent Recovery: Recovering and reusing the extraction solvent significantly reduces emissions and minimizes the need for constant virgin solvent production. Technologies like distillation or adsorption can be employed to achieve high solvent recovery rates.
- Minimizing Solvent Usage: Optimizing the extraction process to use the least amount of solvent possible reduces the environmental burden. This could involve adjusting extraction parameters like temperature and pressure, or employing more targeted solvent delivery methods.
- Energy Efficiency: Evaluating and upgrading equipment to improve energy efficiency throughout the extraction process can significantly reduce the overall environmental footprint. This might involve implementing heat exchangers to recover waste heat or utilizing energy-efficient pumps and motors.
3. Waste Management:
- Wastewater Treatment: Upgrading wastewater treatment facilities is essential. Implementing advanced treatment technologies like membrane filtration or activated carbon adsorption ensures effective removal of contaminants before discharge. Additionally, exploring water recycling options can further reduce freshwater consumption.
- Solid Waste Management: Solid waste generated during the process, such as spent filter media or cleaning materials, needs proper disposal. Following established waste management practices and exploring opportunities for recycling or repurposing these materials can minimize environmental impact.
4. Monitoring and Continuous Improvement:
- Continuous Monitoring: Implementing real-time monitoring systems for emissions, solvent loss, and energy consumption allows for early detection of potential issues and facilitates prompt corrective actions.
- Life Cycle Reassessment: Regularly conducting LCAs throughout the life cycle of the plant helps track progress towards sustainability goals and identify new areas for improvement. This iterative approach ensures continuous advancement towards a more sustainable operation.
The Role of Life Cycle Assessment (LCA):
LCA plays a crucial role in assessing the sustainability of solvent extraction plants. It provides a comprehensive framework for analyzing the environmental impact of the entire process, from raw material extraction to product use and final disposal. By quantifying environmental impacts like greenhouse gas emissions, water consumption, and resource depletion, LCA allows for:
- Identifying hotspots: Pinpointing the life cycle stages with the most significant environmental impact allows for targeted efforts towards improvement.
- Benchmarking: Comparing the environmental performance of different plants or extraction methods facilitates identifying best practices and setting realistic sustainability goals.
- Decision-making: LCA data informs decision-making regarding technology selection, process optimization, and resource allocation to prioritize sustainability initiatives.
Sustainability in solvent extraction is a journey, not a destination. By transitioning to safer solvents, implementing closed-loop systems, optimizing operations, and continuously monitoring and improving practices, solvent extraction plants can significantly reduce their environmental footprint. LCA serves as a valuable tool for guiding this journey, ensuring that the path towards efficient oil processing leads to a more sustainable future.
Conclusion
Solvent extraction stands as a cornerstone process in oil refining operations. Nonetheless, realizing genuine sustainability mandates relentless endeavors to curtail environmental repercussions. Embracing safer solvents, closed-loop systems, and effective wastewater treatment emerges as pivotal initial measures. Furthermore, sustained exploration and advancement in bio-based solvents and alternative extraction techniques offer encouraging prospects for a more sustainable trajectory. The crux of the challenge resides in striking a delicate balance between the imperative for efficient oil processing and the obligation to mitigate our environmental impact.