The Magic of Extraction: How Oil Solvent Extraction Plants Refine the Lifeblood of Lubrication
In the intricate world of machinery, lubricants play a vital role, ensuring smooth operation and protecting essential components from friction and wear. But before these lubricants reach your car engine or industrial gearbox, they undergo a meticulous transformation, often involving a fascinating process called oil solvent extraction. This article delves into the heart of this technology, exploring how oil solvent extraction plants work their magic, the types of base oils they produce, and the benefits they offer for both industry and the environment.
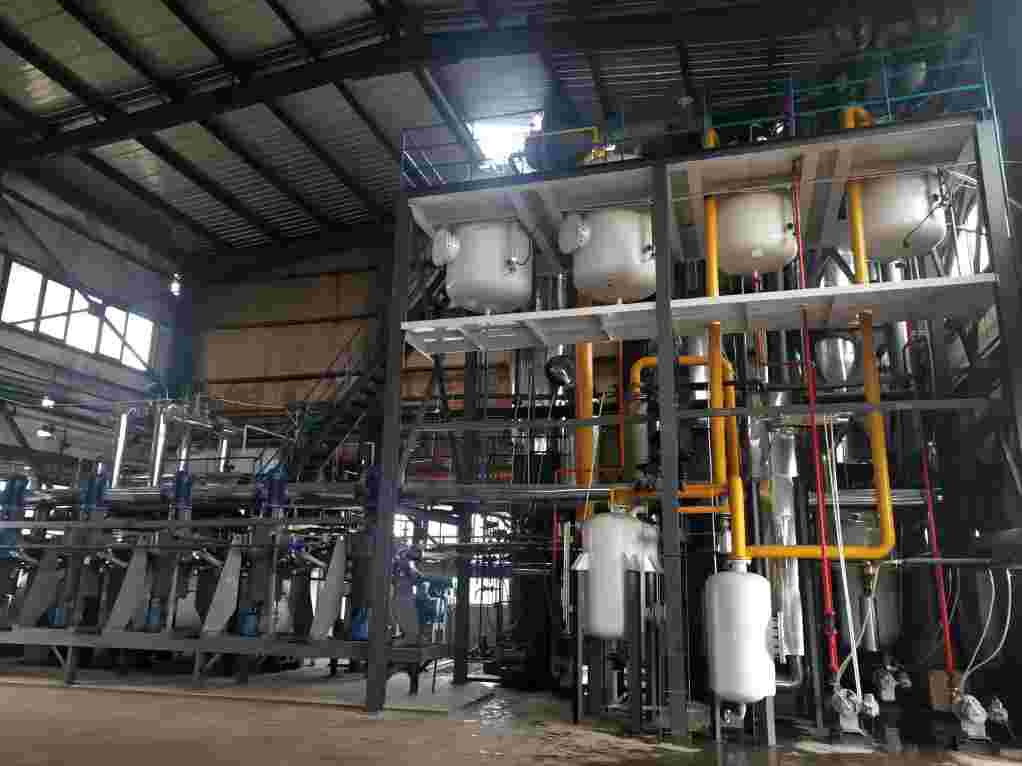
Unveiling the Process: From Crude Oil to Pure Gold
The journey of oil solvent extraction begins with a humble yet crucial ingredient: crude oil distillate. This viscous mixture, derived from refined crude oil, holds the potential for high-quality base oils, the primary building blocks of lubricants. However, impurities like sulfur compounds, asphaltenes, and nitrogen residues hide within, hindering the performance and longevity of the final product. This is where the oil solvent extraction plant steps in, acting as a chemical alchemist.
The first act of this transformation involves feedstock preparation. The distillate undergoes meticulous filtration and cleaning, ensuring no unwanted solids or water interfere with the extraction process. Next comes the crucial step: solvent selection. Each solvent boasts unique properties, and choosing the right one is paramount. Phenol, furfural, and N-methyl-2-pyrrolidone (NMP) are some common players, each targeting specific impurities and influencing the final characteristics of the extracted base oil.
Imagine the feedstock and solvent swirling together in a grand dance within the extractor. Here, the magic happens. The chosen solvent, like a discerning guest at a party, selectively binds with the unwanted impurities, leaving the desirable hydrocarbons untouched. This separation forms the heart of the process, yielding a base oil significantly cleaner and purer than before.
But the extracted oil still clings to its solvent partner. To break this bond, the oil enters the desolventizer, a stage where heat and distillation techniques coax the solvent away. Like a shy perfume evaporating in the air, the solvent leaves behind a refined base oil, ready for its final polishing act.
The distillation unit awaits, a towering apparatus that separates the base oil into distinct fractions based on their boiling points. This final step creates a spectrum of base oils, each boasting unique viscosity and performance characteristics, tailored for specific lubricant applications. Group I base oils, derived from mineral oils, excel in everyday engine oils, while Group II, crafted from hydrocracked oils, find their strength in heavy-duty gear lubricants. Finally, Group III, the crown jewels of this process, are synthetic base oils, renowned for their exceptional thermal stability and wear resistance, demanded in high-performance lubricants for extreme environments.
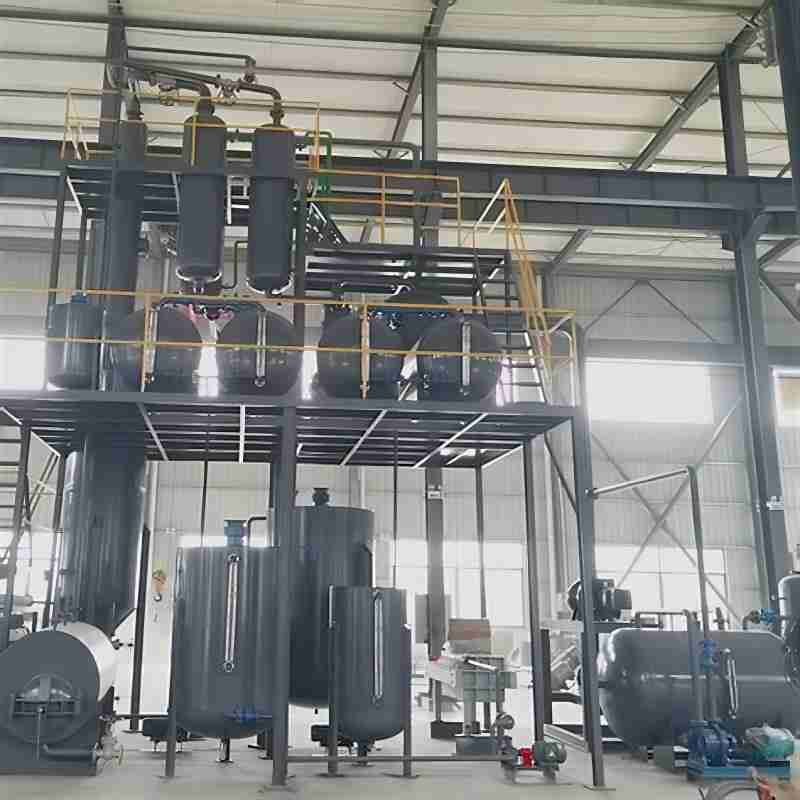
Benefits Worth Extracting: Beyond Purity, a Brighter Future
The magic of oil solvent extraction extends far beyond the enhanced purity of the extracted base oils. This technology unlocks a treasure trove of benefits for both industry and the environment. Firstly, it maximizes the base oil yield. By extracting valuable oils from lower-quality feedstocks, solvent extraction reduces dependence on virgin crude oil, a precious and finite resource. This not only improves resource efficiency but also mitigates the environmental footprint of lubricant production.
Furthermore, solvent extraction paves the way for recycling used oil. This readily available resource, traditionally a burden on waste management systems, can be transformed into high-quality base oils through solvent extraction, offering a sustainable alternative to virgin crude oil use. By closing the loop on the lubricant lifecycle, solvent extraction plants contribute significantly to a circular economy, minimizing waste and reducing environmental impact.
However, the magic of extraction comes with considerations. The capital and operational costs of these plants are significant, requiring careful planning and investment. Additionally, solvent selection and safety demand meticulous attention due to the inherent hazards associated with some solvents. Strict adherence to environmental regulations for emissions and waste disposal is also paramount.
A Look Ahead: The Future of Oil Solvent Extraction
As the world shifts towards sustainability, oil solvent extraction technology continues to evolve, embracing innovation and addressing challenges. Research into bio-based solvents derived from renewable resources like plant oils holds promise for greener extraction processes. Additionally, advancements in membrane separation technology offer alternative methods for selective impurity removal, potentially minimizing solvent use and associated risks.
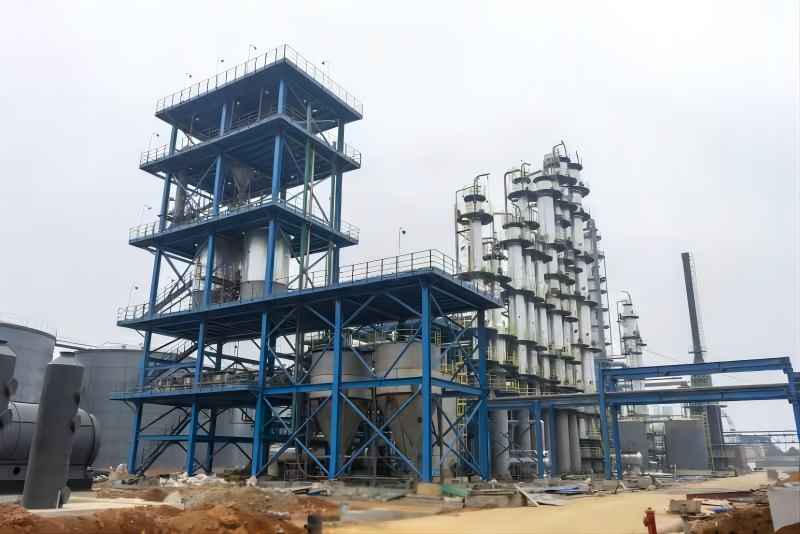
In conclusion, oil solvent extraction plants are not mere industrial giants; they are the skilled alchemists behind the refined lifeblood of our machinery. By transforming crude oil into pure, high-performance base oils, they play a crucial role in ensuring smooth operation, extending equipment lifespan, and minimizing environmental impact. As technology continues to evolve and innovation blossoms, oil solvent extraction stands poised to further enhance its magic, propelling us towards a future where lubrication is both efficient and sustainable.