Common Problems in Lube Oil Blending and How to Overcome?
Lubricant blending is an important process for producing high-quality lubricants for automotive, industrial and marine applications. However, there are still many problems in the lubricant blending process that can affect product quality, consistency and production efficiency.
This article will explore some basic knowledge of lubricant blending, common problems in the blending process and effective solutions. In addition, we will also discuss how advanced lubricant blending plants use technology to optimize production.
Understanding the Basics of Lube Oil Blending
Lube oil blending is a precise manufacturing process that combines base oils with specialized additives to produce high-performance lubricants. These lubricants play a vital role in reducing friction, preventing wear, and extending the lifespan of engines and machinery across automotive, industrial, and marine applications.
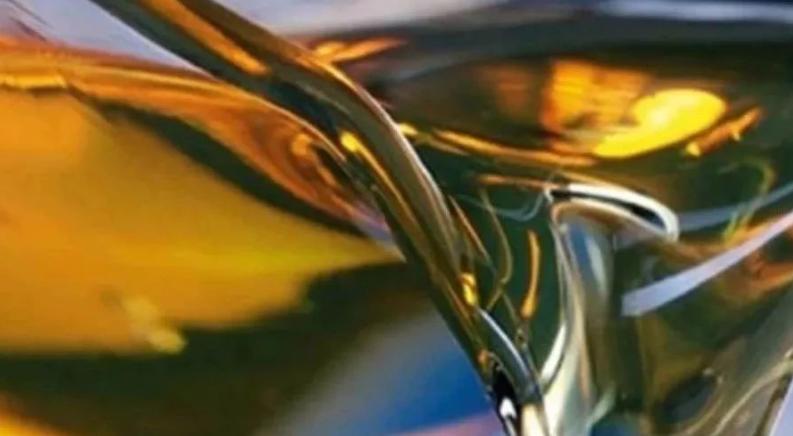
Why Is Lube Oil Blending Necessary?
Different machinery requires lubricants with specific properties to function optimally. It is impossible for a single base oil to meet all the performance expectations, hence the reason for blending. Through accurate mixing of base oils with additives, manufacturers can tailor lubricants to:
- Maintain optimal viscosity in temperature conditions
- Antioxidize and thermally resist degradation
- Reduce friction and wear through anti-wear additives
- Maintain the cleanliness of the engine through detergents and dispersants
- Protect from corrosion and rust
If not blended properly, lubricants can deteriorate under harsh pressures, temperature, or mechanical stress, and do harm to equipment and result in costly downtime.
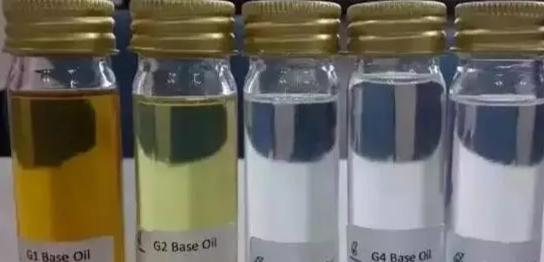
The Lube Oil Blending Process
Careful blending process maintains quality and consistency. The principal steps are:
- Base Oil Selection – Depending on the end-use, manufacturers utilize mineral, synthetic, or semi-synthetic base oils.
- Additive Incorporation – Additives for improving performance (e.g., viscosity index improvers, anti-foaming agents, and extreme pressure additives) are properly measured and blended.
- Homogenization – High-shear mixing ensures additives are mixed well, without separation.
- Quality Testing – The final blend is thoroughly screened for viscosity, flash point, pour point, and oxidation stability before it can be approved.
Blending can be done either by batch processing (for production in smaller quantities) or by inline blending (for continuous bulk operations). High-tech plants have automated systems to achieve higher accuracy and efficiency.
By becoming proficient in these basics, manufacturers are able to create high-quality lubricants that industry standards and customers demand. The second hurdle is avoiding common blending problems—let’s take a look at those next.
Common Problems in Lube Oil Blending
Lube oil blending is an inherently engineered process; nonetheless it often encounters challenges that impede product quality, efficiency and compliance. Below are five of the most frequently experienced difficulties during the blending process:
1. Improper Dosage of Additives
One of the major concerns associated with lube oil blending is inaccurate dosing of additives. Even small variations can have drastic ramifications on product performance and lead to subpar products. Manual measurement or poorly calibrated dosing systems often result in over or under dosing which inevitably requires costly rework or waste removal processes.
2. Uneven Blend Quality
Achieve consistent product results through uniform mixing of base oils and additives. Variations in base oil characteristics, fluctuating temperatures or inadequate mixing times may lead to viscosity variations that result in viscous or visceral problems – often leading to failed quality tests or product rejection.
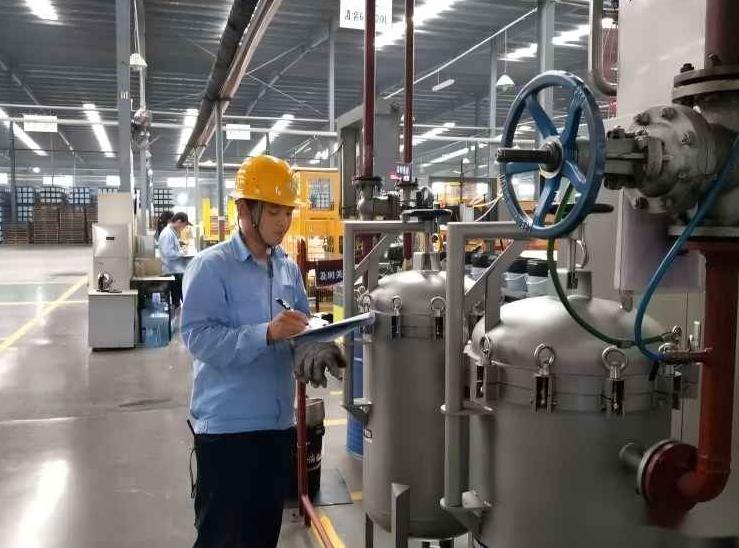
3. Cross-Contamination
Cross-contamination between product batches can be an ongoing problem in plants without automatic cleaning systems, particularly where residue from previously blended batches remains in tanks, pipelines or pumps – leaving dangerous off-spec products that cannot be sold on the market.
4. Temperature Control Issues
Achieving proper temperature control when it comes to the blending process is of great importance, since many additives need certain temperatures in order to activate and disperse properly. Any insufficient heating or cooling systems could result in poor solubility, uneven distribution or incomplete reactions and consequently compromise lubricant quality.
5. Lack of Real-Time Monitoring
Without real-time information on key process parameters – including flow rates, viscosity and temperature–blending operators tend to react rather than anticipate process deviations; this makes correcting problems harder before they ripple throughout a batch.
How to Overcome Lube Oil Blending Problems
In order to produce high-quality and promote operational efficiency, lube oil manufacturers must overcome blending challenges on a regular basis through preventive measures. The five best practices for overcoming blending challenges in lube oil are outlined below:
1. Automate Additive Dosing Systems
A shift from manual to automatic dosing increases accuracy and consistency significantly. Dosing systems now use flow meters, PLC controls, and precision pumps to deliver precise volumes of additives with minimal human error and reduced product waste. Automation ensures that each batch has highly controlled formulation specifications.
2. Implement Real-Time Monitoring and Control
installing sensors and control systems to track real-time temperature, flow rate, and viscosity data allows operators to see deviations right away. SCADA systems embedded in equipment can make automatic changes to avert off-spec production from happening.
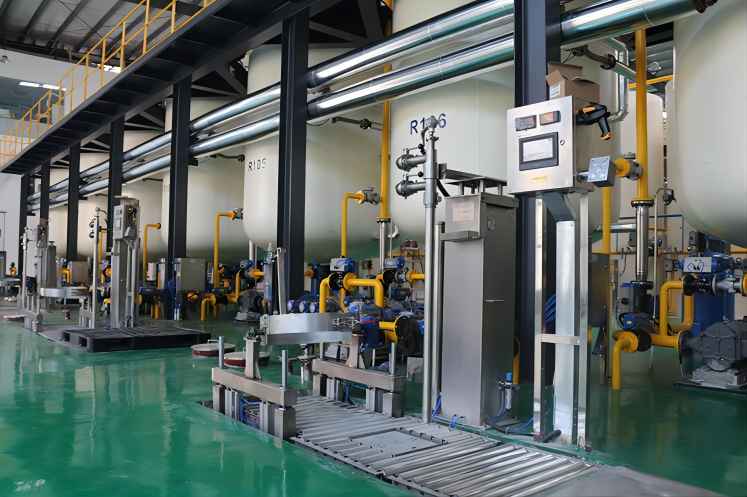
3. Standardize Operating Procedures
Maintaining good Standard Operating Procedures (SOPs) helps in maintaining consistency in the blending processes. SOPs should cover raw material handling, blending order, and sanitation methods. Engaging the staff in frequent training on these procedures helps in having a consistent approach to every batch.
4. Employ Clean-in-Place (CIP) Systems
CIP technology automates the cleaning of blending tanks and pipelines from batch to batch, preventing cross-contamination hazards. This reduces downtime, maintains product purity, and achieves highest process efficiency without the need for human intervention.
5. Regular Equipment Maintenance and Calibration
Periodic maintenance of blending equipment and regular calibration of dosing devices and sensors are important to ensure accurate operation. Preventive schedule maintenance prevents unexpected breakdowns, ensures accuracy, and extends the life of blending infrastructure.
Through these practices, lube oil manufacturers can reduce blending errors significantly, enhance the quality of their products, and simplify operations for long-term sustainability.
Advanced Technology: Lube Oil Blending Plant
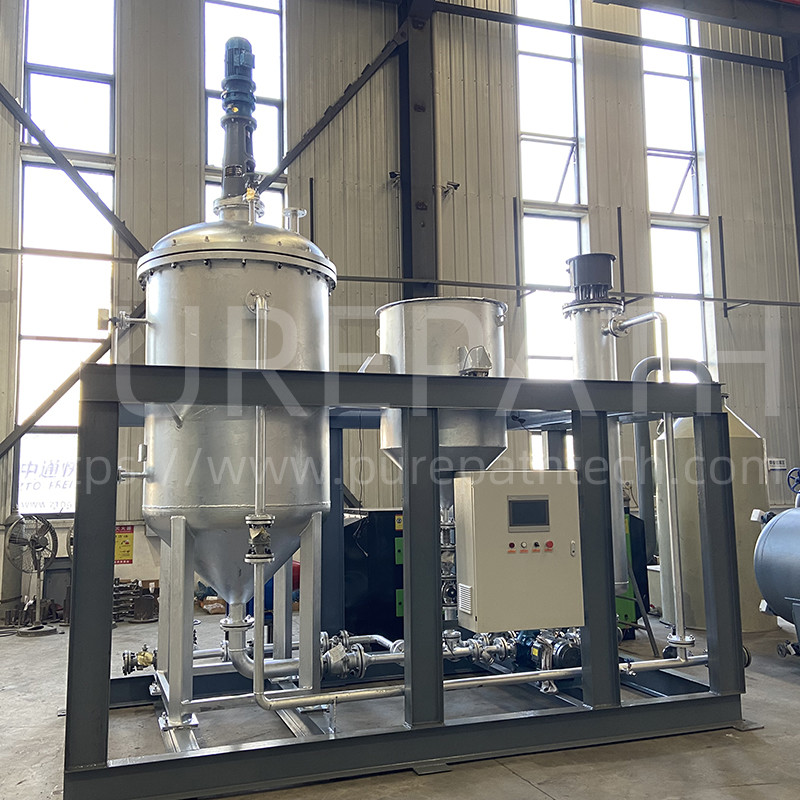
Modern Lube Oil Blending Plants are revolutionizing lubricant production through automation, digitalization and integrated control systems. These state-of-the-art facilities aim to maximize productivity while remaining precise with complex formulations; featuring features like recipe-driven batch control, material handling automation and centralised data logging to increase both speed and accuracy across operations.
Cutting-edge blending systems also incorporate digital twins and remote diagnostics, providing operators with real-time simulation of blend outcomes, monitoring of performance, and troubleshooting issues in real time to reduce downtime and enhance decision-making capabilities. Furthermore, energy-efficient mixing technologies combined with smart utility management help minimize environmental impact as well as operational costs.
Advanced Lube Oil Blending Plants enable manufacturers to not only meet rising industry requirements, but also future-proof their operations against regulatory changes and supply chain fluctuations – offering better quality, faster response times, and increased sustainability.