How Crude Oil Is Separated into Fractions
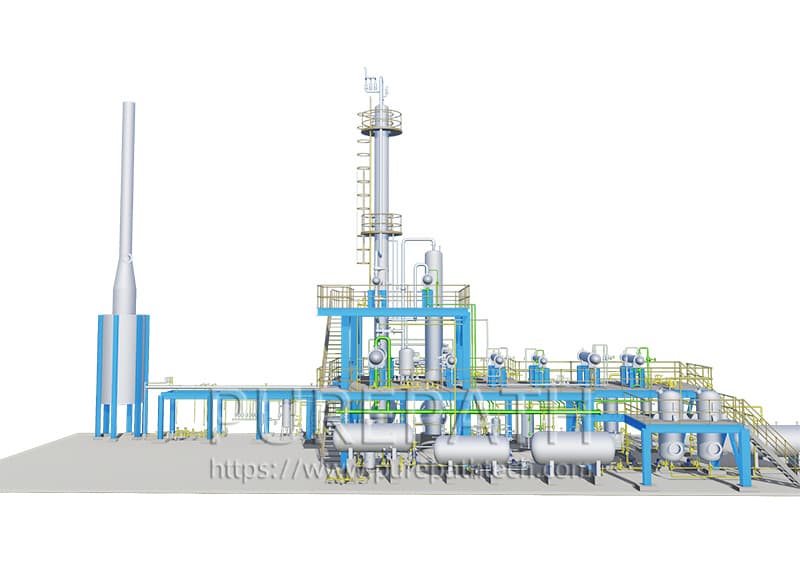
In my years working with oil refining clients, one question keeps coming up: How do you separate crude oil into useful products? The answer isn’t just “heat and separate.” It’s a controlled transformation — from an unrefined black liquid into fuels, lubricants, chemicals, and asphalt — using some of the most finely tuned industrial systems ever built.
This article walks you through that journey, not as a guidebook, but as a real-world lens on how fractionation is engineered, what technologies drive it, and why it matters for buyers making capital investment decisions in the oil refining space.
What Is Crude Oil, and What Does It Contain?
Crude oil is a naturally occurring mixture of hydrocarbons formed over millions of years. But what makes it commercially valuable is not what it is — it’s what can be extracted from it.
Crude oil contains a complex mix of hydrocarbons with different molecular weights, boiling points, and chemical behaviors. These include:
- Light gases like methane, propane, and butane
- Naphtha and gasoline-range hydrocarbons
- Middle distillates like kerosene and diesel
- Heavy fractions are used in lubricants, fuel oil, and asphalt
No refinery processes crude oil as-is. To unlock its value, it must be separated into distinct product streams — each with a specific market use.
How Crude Oil Is Separated into Fractions
It’s Not Just Heating. It’s Fractional Mastery.
Many explanations oversimplify crude oil separation as “heating and collecting vapors.” In reality, it’s about managing molecular behavior under strict thermodynamic conditions — continuously and at scale.
Here’s how we approach it:
- Every hydrocarbon in crude oil has a unique boiling point.
- When the oil is heated, those components evaporate at different temperatures.
- A specialized tower, called a fractionating column, allows these vapors to rise and condense at different levels based on temperature gradients.
- The entire system is engineered to allow controlled condensation and withdrawal at precise points.
This is not a batch process — it’s a continuous, integrated system designed for high efficiency and consistent throughput.
Core System Architecture: Beyond the Column
When buyers look at crude distillation systems, they often start with tower size or daily capacity. But what matters is how the entire thermal and mechanical ecosystem is engineered:
Feed Heat Integration
Before entering the furnace, crude oil is preheated using internal heat exchangers, typically by recovering heat from product streams. This significantly reduces external fuel consumption and improves energy balance.
Crude Furnace
Here, oil is heated under controlled conditions — not just to a boiling point, but to a precise temperature window that allows partial vaporization without cracking the heavier molecules. This is where thermal input is calibrated for maximum separation efficiency.
Atmospheric Distillation Column
This is the heart of the system. A vertical vessel, often 30–60 meters tall, maintains a temperature gradient from bottom (hot) to top (cool). Internally, it contains trays, structured packing, or valve decks, enabling vapor-liquid contact and phase separation.
At each level, specific hydrocarbons condense and are withdrawn as side draws.
Overhead Condenser and Reflux System
Vapors reaching the top are condensed, and part of the liquid is recycled back into the tower (reflux) to sharpen the separation zone and improve product purity.
Vacuum Distillation Unit (Optional)
Heavier fractions from the bottom may enter a vacuum distillation column, where pressure is reduced to allow further separation without high-temperature degradation.
Solution Customization: No Two Refineries Are the Same
Every crude distillation unit (CDU) is built based on unique operational needs:
- Feedstock profile (light crude vs. heavy crude)
- Target product yield (more diesel? less naphtha?)
- Energy integration with downstream units (hydrotreaters, reformers)
- Local environmental compliance and emissions targets
When we work with clients, we focus less on “buying a tower” and more on engineering a yield strategy — aligning your product slate with market demand, energy costs, and operational goals.
Main Applications of Crude Oil Fractions After Distillation
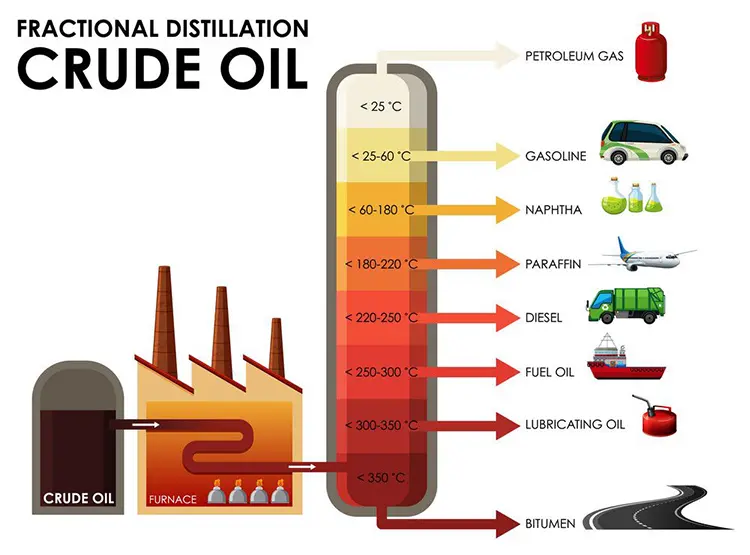
Once separation is complete, each fraction serves a specific role in global supply chains — from transportation to infrastructure, from chemicals to power generation.
Fraction | Boiling Range (°C) | Typical Applications |
LPG | <40 | Bottled gas, chemical feedstock for petrochemicals |
Light Naphtha | 40–100 | Gasoline blending, reforming, olefin production |
Heavy Naphtha | 100–160 | Aromatics extraction, gasoline blending |
Kerosene | 160–250 | Jet fuel, heating oil, lamp oil |
Diesel | 250–350 | Transportation fuel, generators, marine diesel |
Atmospheric Residue | >350 | Feedstock for vacuum distillation, bitumen, fuel oil |
Vacuum Gas Oil (VGO) | 350–500 | FCC feedstock, lube base oils, hydrocracking |
Asphalt/Bitumen | Residual | Road construction, waterproofing, industrial coatings |
Each product stream can be further treated or converted depending on final demand and refinery configuration.
Final Thoughts
To the untrained eye, a distillation tower appears to be a simple steel column. But to us — engineers, buyers, plant managers — it’s a precision tool designed to unlock commercial value from natural resources.
A well-designed fractionation system is not just about separating oil. It’s about:
- Building reliability into long-term refinery operations
- Maximizing yield from each barrel
- Optimizing thermal efficiency and reducing carbon intensity
- Aligning your plant’s output with product economics