Comparing Used Oil Re-Refining and Waste Oil to Diesel Conversion
The global lubricant market, exceeding 40 million metric tons annually, generates a substantial volume of used oil, posing both environmental and economic challenges. Improper disposal of used oil contaminates soil and waterways, while its untapped potential as a valuable resource remains unrealized. This article delves into two prominent avenues for used oil valorization: re-refining and waste oil to diesel conversion, and analyzing their respective processes, outputs, and implications.
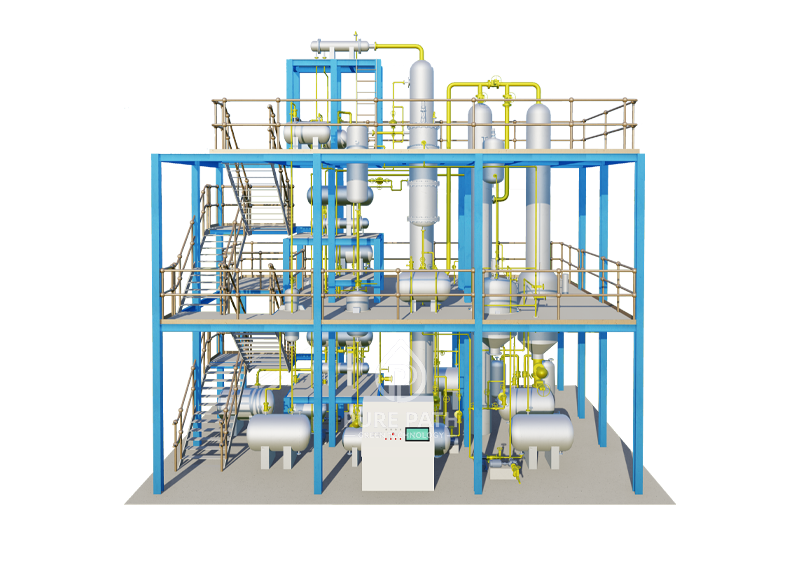
Used Oil Re-Refining: Reclaiming the Value
Used oil re-refining meticulously transforms contaminated oil back into high-grade lubricating oil, minimizing environmental impact and resource depletion. The process entails a multi-stage purification and optimization journey:
1. Pre-Treatment
- Centrifugation and Filtration: High-speed centrifuges remove larger contaminants like metal particles and sludge. Subsequent filtration eliminates finer impurities like dust and residual solids.
- Dehydration: Advanced dehydration techniques, such as vacuum distillation or membrane separation, remove emulsified water, preventing premature oil degradation and ensuring optimal lubrication performance.
2. Vacuum Distillation
- Fractional Separation: The pre-treated oil undergoes controlled heating under vacuum conditions. This separates the oil into distinct fractions based on their boiling points. Lighter components like gasoline and diesel are distilled off, while heavier base oil fractions, the primary target for re-refining, remain.
- Flash Evaporation: Further separation within the base oil fraction can be achieved through flash evaporation, yielding distillates with specific viscosity ranges for targeted applications.
3. Hydrotreating and Decolorization
- Hydrotreating: The base oil fractions undergo a catalytic hydrogenation process, reacting with sulfur, nitrogen, and other impurities to form stable, non-corrosive compounds. This significantly improves the oil’s oxidation resistance and thermal stability.
- Decolorization: Adsorption technologies like clay or activated alumina remove unwanted colorants and improve the oil’s clarity, enhancing its visual appeal and indicating effective purification.
4. Additive Blending and Quality Control
- Precise Blending: A meticulous blend of carefully formulated additives is incorporated into the purified base oil. These additives enhance properties like viscosity, friction reduction, and wear resistance, tailoring the oil to specific performance requirements and engine types.
- Stringent Quality Control: Throughout the process, rigorous analytical testing ensures the re-refined oil meets or exceeds stringent industry standards for chemical composition, viscosity, and performance parameters.
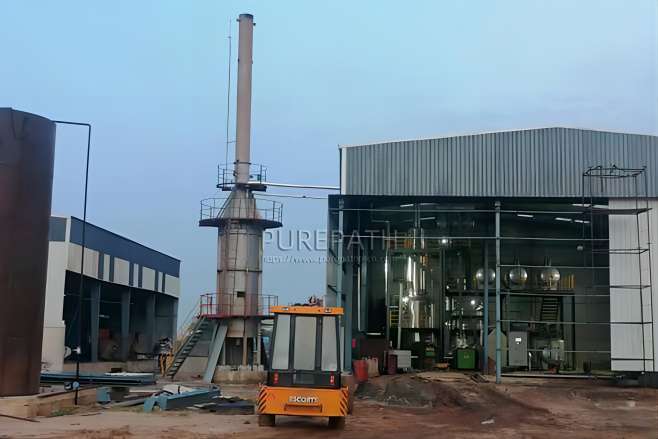
What Are the End Products of Used Oil Re-Refining?
The culmination of this intricate process is high-quality lubricating oil, indistinguishable in performance from virgin oil. This re-refined oil possesses the viscosity, oxidation resistance, and wear protection characteristics necessary for diverse applications, including:
- Automotive Lubrication: Engine oil, gear oil, transmission fluid
- Industrial Lubrication: Hydraulic fluids, compressor oils, turbine oils
- Marine Lubrication: Engine oils, gear oils, hydraulic fluids
The Benefits of Used Oil Re-Refining
Re-refining offers a plethora of environmental and economic advantages:
- Resource Conservation: By regenerating used oil, re-refining reduces dependence on virgin oil extraction, minimizing the environmental impact associated with drilling, refining, and transportation.
- Pollution Reduction: Improper disposal of used oil can contaminate soil and waterways. Re-refining diverts used oil from landfills and incineration, mitigating environmental pollution.
- Circular Economy: Re-refining promotes a circular economy for lubricants, minimizing waste generation and maximizing resource utilization.
- Economic Viability: Re-refined oil offers a cost-effective alternative to virgin oil, benefitting both consumers and businesses.
The Drawbacks of Used Oil Re-Refining
While re-refining boasts significant advantages, it also presents certain challenges:
- Complexity and Cost: The multi-stage process requires specialized equipment, skilled personnel, and strict quality control measures, leading to higher operational costs compared to simpler methods.
- Feedstock Limitations: Not all types of used oil are suitable for re-refining. Highly contaminated or blended oils may require extensive pre-treatment or may not be optimal for high-quality lubricant production.
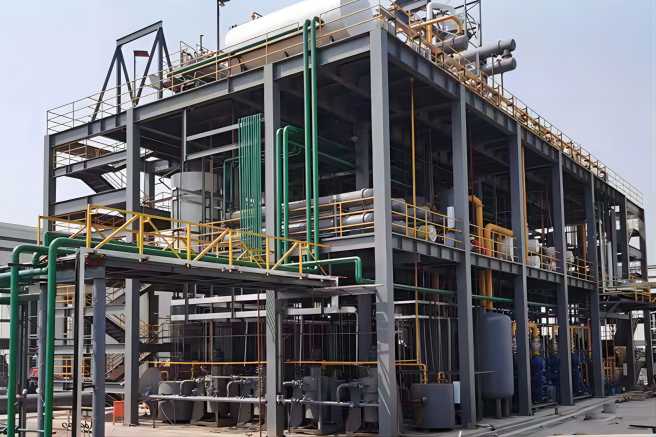
Waste Oil to Diesel: A Straightforward, Yet Delicate, Route
Waste oil to diesel conversion offers a more direct approach to valorizing used oil, transforming it into a fuel source through a simplified process. However, this efficiency comes with caveats necessitating careful consideration:
1. Filtration
- Coarse Filtration: Initial filtration employs large-mesh screens or mechanical separators to remove large debris like metal chips, gasket fragments, and other coarse contaminants. This protects downstream equipment and ensures consistent fuel flow.
- Optional Fine Filtration: Depending on the feedstock and desired fuel quality, additional fine filtration steps may be implemented to remove finer particles like soot and sludge.
2. Distillation
- Single-Stage Distillation: Unlike the multi-stage vacuum distillation of re-refining, waste oil to diesel conversion typically utilizes a single-stage atmospheric distillation process at lower temperatures. This separates the lighter, volatile components from the heavier residues.
- Flash Fractionation: Further segregation within the lighter fractions can be achieved through flash fractionation, yielding distillates with specific boiling point ranges suitable for different applications.
3. Treatment and Fuel Upgradation
- Water Removal: Residual water content can be detrimental to fuel stability and combustion efficiency. Techniques like centrifuging or coalescing filters remove emulsified water, ensuring a dry fuel product.
- Neutralization and Additives: Depending on the feedstock and desired fuel properties, neutralization may be employed to adjust the acidity level. Additionally, specific additives can be blended to improve cetane number (ignition quality), lubricity, and corrosion resistance.
What Are the End Products of the Waste Oil to Diesel Conversion?
The resulting fuel, often referred to as “waste oil diesel” or “pyrolysis diesel,” possesses characteristics distinct from both virgin diesel and fully re-refined oil:
- Lower Quality: Compared to virgin diesel, waste oil diesel typically exhibits lower cetane number, higher viscosity, and potentially higher sulfur and nitrogen content. This necessitates engine modifications or blending with virgin diesel for optimal performance and emissions compliance.
- Variable Properties: The fuel quality can vary significantly depending on the feedstock and processing parameters. Careful analysis and adjustment may be necessary to ensure compatibility with specific engines and emission standards.
The Benefits of Waste Oil to Diesel Conversion
Waste oil to diesel conversion offers several advantages:
- Process Simplicity: The single-stage distillation and basic treatment steps require less equipment and expertise compared to re-refining, making it a more accessible option for smaller-scale operations.
- Feedstock Flexibility: Waste oil to diesel can handle a wider range of used oil types, including heavily contaminated or blended oils, which may not be suitable for re-refining.
- Cost-Effectiveness: The simpler process and lower equipment requirements result in lower operational costs compared to re-refining, making it a more cost-competitive option for certain applications.
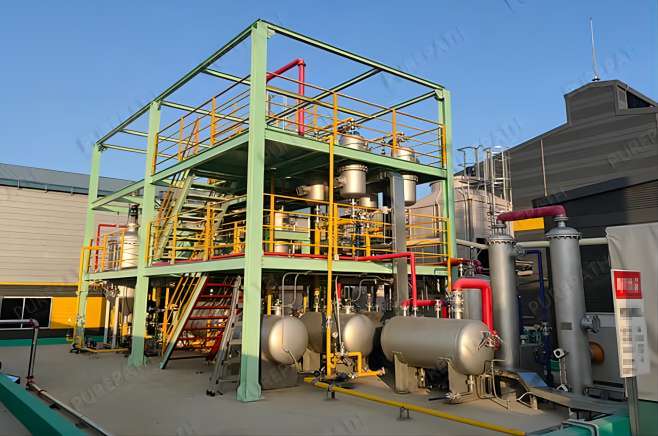
The Drawbacks of Waste Oil to Diesel Conversion
However, the lower fuel quality and operational intricacies introduce specific challenges:
- Emission Concerns: Waste oil diesel can have higher emissions of particulate matter and other pollutants compared to virgin diesel, necessitating careful consideration of environmental impact and potential regulatory compliance challenges.
- Engine Issues: Improperly processed or used waste oil diesel can damage engine components due to factors like higher viscosity, higher ash content, and the potential presence of corrosive impurities. This necessitates proper fuel treatment, blending, and engine compatibility evaluations.
- Fuel Quality Variability: The fuel quality produced through waste oil to diesel conversion can exhibit higher variability compared to commercially available fuels, requiring close monitoring and potential adjustments to fuel blends and engine settings.
Here’s a table summarizing the key differences:
Feature | Used Oil Re-Refining | Waste Oil to Diesel |
Process | Complex, multi-stage | Simpler, single-stage |
Output | High-quality lubricating oil | Lower-quality diesel-like fuel |
Benefits | Conserves resources, reduces pollution, creates valuable product | Simpler, handles wider range of oils |
Drawbacks | Simpler, handles a wider range of oils | Lower quality fuel, engine modifications, potential emissions |
Conclusion: Choosing the Optimal Pathway
The choice between re-refining and waste oil to diesel conversion hinges on several factors, including the desired output, available resources, and environmental considerations. For applications demanding high-quality lubricating oil, re-refining remains the undisputed champion. Its stringent purification processes and stringent quality control measures translate to superior performance and environmental benefits. Conversely, waste oil to diesel conversion presents an attractive alternative when cost-effectiveness and wider feedstock compatibility are paramount. However, its lower fuel quality and potential environmental concerns necessitate careful consideration and responsible implementation.
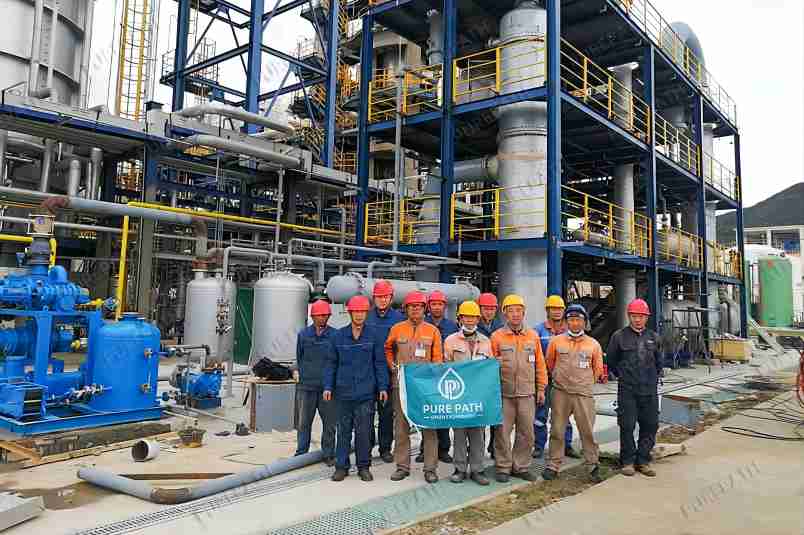
Ultimately, both re-refining and waste oil to diesel conversion offer valuable pathways for used oil valorization. By critically evaluating their respective strengths and limitations, stakeholders can navigate this complex landscape and choose the most suitable option for their specific needs, paving the way for a more sustainable and resource-efficient future.