How to Dispose of Lube Oil Blending for Different Classes of Unqualified Products?
Lube oil blending is a complex process that involves many steps, from the selection of raw materials to the final product. During this process, there are many opportunities for errors to occur, resulting in non-conforming products. When this happens, it is important to take steps to dispose of the non-conforming product in a safe and environmentally responsible manner. In this article, we will discuss some disposal methods of lubricant blending for different classes of unqualified products.
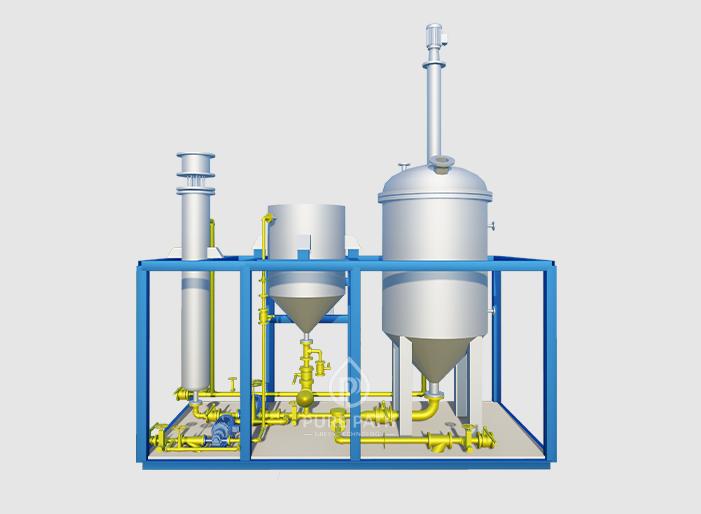
Disposal methods for different classes of lube oil blending non-conforming products
1. Disposal of Unqualified Viscosity
The viscosity of lubricants has a great influence on the fluidity and the thickness of the oil film formed between the friction surfaces. Lubricants with higher viscosity form a thicker oil film between the friction surfaces, which has good lubrication performance, but consumes more power in overcoming friction resistance, and has poor fluidity. In order to save energy and reduce fuel consumption, low-viscosity finished oil is generally used, but if the viscosity is too low, the oil film is too thin and easy to break, causing wear. Therefore, it is necessary to control the appropriate viscosity index.
The main reasons for unqualified viscosity are as follows:
- Formula calculation error, or formula input error in the computer;
- Measurement equipment failure or material temperature is too low, resulting in large measurement errors;
- Process operation errors, such as mis-feeding oil;
- Mixing is not uniform;
- Pipeline storage treatment is not clean;
- Process parameters are not controlled properly.
Disposal methods:
- Check whether the formula is correct, such as the variety and batch number;
- Check the material balance to verify whether the material usage is in line with the formula requirements;
- Check the mixing equipment for abnormalities;
- Check whether the flow meters, scales, and oil gauges used are faulty or damaged;
- Before feeding, confirm and consider the impact of the oil in the pipeline, and whether necessary treatment has been carried out.
- If the unqualified value is not significantly different from the standard, and no clear unqualified reason has been found, it can be mixed again and re-analyzed;
- According to the high or low of the unqualified value, add the appropriate amount of light, heavy components and additives in the formula to keep the oil performance from being reduced due to adjustment;
- When adjusting unqualified products, if two or more items are unqualified, it is necessary to comprehensively consider and analyze whether the two items are related to each other.
2. Disposal of Unqualified Pour Point
The main reasons for unqualified pour points are as follows:
- Raw material component metering error is large;
- Formula error or formula input error in the computer;
- The dilution of the pour point depressant is not uniform, the ratio is out of control, or the calculation is wrong;
- The mixing of oil products is not uniform;
- The pour point depressant is of poor quality or the base oil is not receptive.
The analysis, disposal methods of unqualified lube oil products:
- Check the formula, material mixing records for accuracy;
- Check the material balance to verify whether the material usage is in line with the formula requirements, especially whether the usage of pour point depressant is normal;
- Check the pour point of the oil mixed at the same time or adjacent time to see if it is abnormal;
- Check whether the pour point of the raw oil is too high, resulting in the pour point of the blended oil being unqualified;
Adjustment: Add pour point depressant, mix evenly, and pay attention to the oil product mixing temperature meets the process requirements. If the unqualified value is within the analysis error range, and no clear unqualified reason has been found, it can be mixed again and re-analyzed.
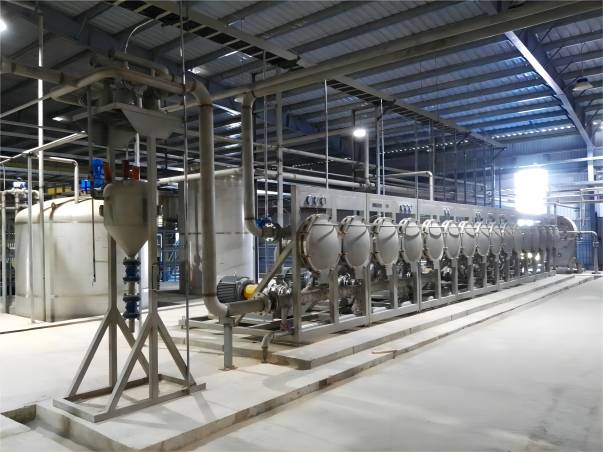
3. Disposal of Unqualified Low-temperature Dynamic Viscosity
Low-temperature dynamic viscosity is one of the important performance indicators of lubricants that reflect the low-temperature performance of lubricants. The low-temperature performance of the base oil is mainly determined by the distillation fraction and viscosity index of the base oil used, and the low-temperature performance of the finished oil is related to the proportion of light and heavy components in the formula, the structure composition and proportion of viscosity index improver, etc. If the low-temperature performance of the lubricant is poor, the lubrication system cannot provide appropriate lubrication under low-temperature conditions, resulting in serious wear of moving parts, and even the pump cannot start.
The main reasons for unqualified low-temperature dynamic viscosity are as follows:
- The low-temperature performance of the base oil is poor;
- The proportion of the formula is unreasonable;
- The finished oil viscosity is too high;
- Raw material component metering error is too large;
- The blended oil is not mixed uniformly.
Disposal methods for unqualified products:
- If the unqualified value is not significantly different from the standard, and no clear unqualified reason has been found, it can be mixed again and re-analyzed;
- You can appropriately reduce the base oil viscosity, and pay attention to adding additives in proportion;
- If the unqualified value is considerably different from the standard requirements, adjust the formula, appropriately increase the proportion of light components in the formula, or decrease the proportion of heavy components, but pay attention to control the mixed viscosity of the base oil not to be too low. When adding, generally choose low-temperature performance II or III base oil, and add additives at the same time.
4. Disposal of Unqualified Total Base Number
The cleaning dispersants added to the oil are mostly alkaline. Measuring the total base number can indirectly indicate the amount of additives contained. The total base number is generally used as an important quality index for internal combustion engine oil. On the one hand, due to the oxidation and decomposition of additives, internal combustion engine oil gradually loses its effectiveness; on the other hand, the acids generated by oxidation neutralize alkaline additives, so the total base number gradually decreases. Therefore, measuring the total base number can also judge the degradation of additives, and the decrease in the total base number can be used to determine the oil change cycle.
The main reasons for the unqualified total base number are:
- Raw material component metering error is too large;
- Formula error, or formula input error in the computer;
- The alkalinity of the additive itself is low;
- The blended oil is not mixed uniformly.
Disposal methods for unqualified products:
- Analyze the alkalinity of the additive, calculate the difference between the theoretical value and the standard value, and judge whether the alkalinity of the additive meets the requirements;
- Analyze whether the indicators of the base oil meet the requirements, such as the acid value;
- Check whether the metering equipment is normal;
- Adjustment: Add base oil or additives, mix evenly; If the alkalinity of the additive itself is unqualified, consider adding a reinforcing agent.
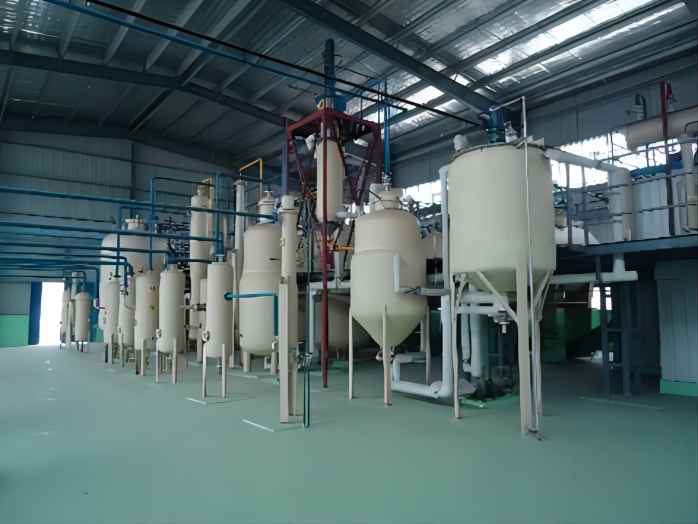
5. Disposal of Unqualified Ash Vontent
The ash content is mainly composed of metal salts and metal oxides generated after combustion. During the production, storage, transportation, and use of oil, factors such as metal salt corrosion generated by equipment, pipelines, and metal containers, iron rust generated by oxidation, paint dissolution, and dust pollution contribute to the ash content. Metal salts in additives are also a source of ash content. The presence of ash will increase the carbon deposits in the process of using lubricants, and excessive ash content will also cause wear of mechanical parts. For oil products that do not contain additives, the ash content can be one of the indicators to check whether the refining is normal. If there are residues of metal salts and white clay in the refining process, the ash content will increase. For lubricants with additives, measuring the ash content can indirectly indicate the content of additives.
The main reasons for unqualified ash content are:
- Raw material component metering error is too large;
- Formula error or formula input error in the computer;
- Base oil carries metal salts and white clay remaining from the refining process;
- Metal rust and slag generated by construction or corrosion of oil tanks and pipelines;
- The blended oil is not mixed uniformly;
- The mixing system contains residual components outside the formula, polluting the oil product.
Disposal methods for unqualified ash content:
- Check if the additive dosage is too high;
- Analyze whether the mechanical impurities in the oil exceed the standard;
- Analyze whether the ash content of the base oil is too high;
- Adjustment: If the ash content is low, add additives, mix evenly; If the ash content is high, increase the blending output, reduce the ash content;
- Check the tank cleaning records, whether the tank has not been cleaned for a long time, and check whether there is rust falling off from the tank top and wall.
6. Disposal of Unqualified Anti-emulsification
Anti-emulsification is the ability of lubricants to resist mixing with water to form emulsions. Oil products with large surface tension are not easy to form emulsions, but contain more mechanical impurities, soaps, acids, and oil sludge in the oil. These surface-active substances seriously destroy the surface tension of the oil product, making it easy to emulsify in water. Lubricants with good anti-emulsification properties are not easily emulsified or form emulsions that separate very quickly even after mixing and stirring with water. In the presence of water, poor anti-emulsification lubricants are easily emulsified, and their oxidation stability is also poor. Anti-emulsification is an important quality indicator for turbine oil. Turbine oil emulsion destroys the oil film, increases friction, wear, and corrosion.
Reasons for unqualified anti-emulsification:
- Impurities or polar substances mixed into the base oil, resulting in unqualified anti-emulsification of the finished product;
- The base oil itself has poor anti-emulsification properties;
- When changing oil, the polar substances in the additives of the previous oil contaminate the subsequent oil in the mixing tank, leading to unqualified anti-emulsification;
- Base oil is contaminated during transportation, resulting in unqualified anti-emulsification;
- Oil tanks are not cleaned properly after long-term use or storage, leading to excessive impurities and affecting the oil’s anti-emulsification.
Disposal methods for unqualified anti-emulsification:
- Add a demulsifier and mix evenly;
- Blend in batches with the same type of oil.
Preventive measures:
- Pay attention to the analysis and selection of raw materials;
- For oils with significant differences, clean or rinse the oil tank before using it for a different oil, especially when blending turbine oil, to avoid contamination from other additives;
- Reduce the entry of mechanical impurities, oil sludge, etc. into the oil product.
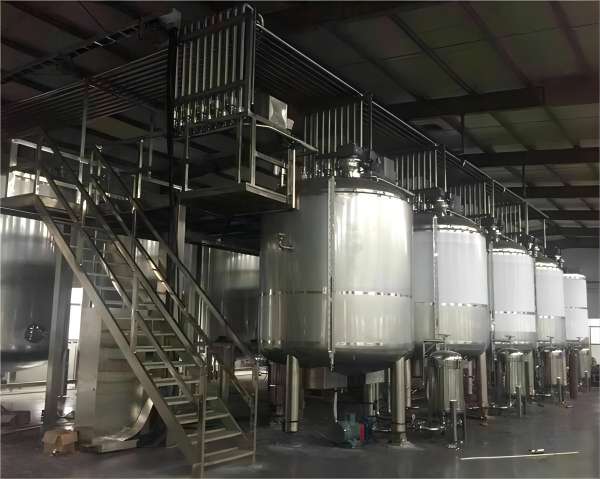
7. Disposal of Unqualified Anti-foaming
In practical use, lubricants generate air bubbles due to vibration, stirring, and other factors. If the anti-foaming property of the oil product is poor, the large number of bubbles formed cannot be broken quickly, which will affect the lubrication performance, accelerate its oxidation and deterioration; destroy the oil film, increase equipment wear; cause air lock in the lubricant circulation system, interrupt oil supply, hinder lubrication, and affect pressure transmission in hydraulic oil; a large amount of foam in turbine oil causes the oil tank to overflow, prevents the oil pressure from rising, affects the circulation, destroys the oil film, and causes vibration and wear. Therefore, good anti-foaming performance is required for oil products. Generally speaking, the higher the viscosity of the oil product, the worse the anti-foaming property. Although silicone anti-foaming agents can effectively improve the surface anti-foaming performance of oil products, they can also worsen the air release performance in the oil. Some non-silicone anti-foaming agents not only have good defoaming effects, but also have minimal impact on the air release performance of oil products.
Reasons for unqualified anti-foaming:
- Insufficient anti-foaming agent addition;
- The type of anti-foaming agent does not match the oil product;
- If using dimethyl silicone anti-foaming agent, the dilution ratio may be inaccurate or the mixing is not uniform;
- The anti-foaming agent is not evenly dispersed in the oil.
Disposal methods for unqualified anti-foaming:
- Add an anti-foaming agent, but control the total amount to avoid worsening the anti-foaming property;
- Choose different types of anti-foaming agents for different oil products, such as non-silicone types for hydraulic oil which also helps with air release;
- Silicone and non-silicone anti-foaming agents can be used together, but require small-sample trials;
- Extend the oil product mixing time to allow the anti-foaming agent to disperse fully, and re-analyze.
8. Disposal of unqualified air release
Foaming refers to the tendency to generate foam and its stability, while air release refers to the ability of an oil product to release air bubbles suspended or dispersed in the oil. In the lubricant circulation system, it is inevitable to bring in some air. Air in the oil product exists as two forms: larger bubbles and mist-like small bubbles. Larger bubbles can quickly rise to the surface of the oil product, while bubbles with a diameter smaller than 0.5mm rise to the surface of the oil product at a slower speed. These small bubbles are mist-like bubbles. The mist-like bubbles in the oil product will destroy the oil film, produce air resistance, and cause insufficient oil supply, noise, and vibration of the machinery, affecting system pressure transmission, causing malfunctions and increased friction in the hydraulic system, oil temperature rise, accelerating oil product oxidation, generating sediment and sludge, clogging filters, and impacting equipment life. Therefore, this indicator is very important for the actual use, storage, and transportation of lubricants.
Reasons for unqualified air release:
- Primarily related to the air release performance of the base oil, selecting a suitable base oil is crucial.
- The degree of dispersion of the anti-foaming agent greatly affects the addition effect.
- The temperature and viscosity of the oil product are related to the lifespan of the air bubble in the oil (the time it takes from bubble formation to complete disappearance). Data shows that the lifespan of the bubble decreases exponentially with increasing temperature and increases exponentially with increasing viscosity. Therefore, lowering the oil product temperature and increasing the oil product viscosity are beneficial for air release.
Disposal methods for unqualified air release:
- Choose a suitable base oil, such as lower viscosity base oil with better air release properties;
- Increase the oil product temperature, which is beneficial for bubble dissipation;
- Add an anti-foaming agent, but control the total amount to avoid worsening the air release property;
- Extend the oil product mixing time to allow the anti-foaming agent to disperse fully, and re-analyze.
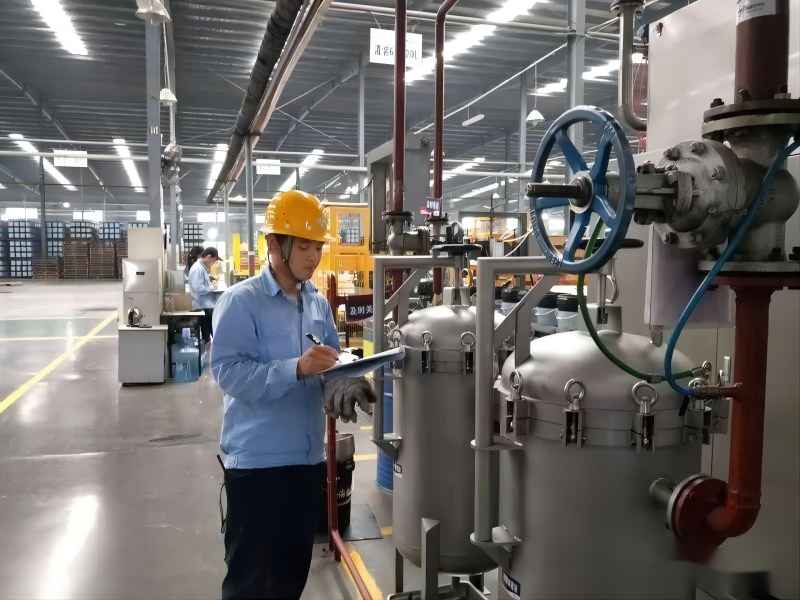
Conclusion
The disposal methods for unqualified lube oil blending vary depending on the specific class of non-conforming products. A comprehensive understanding of the potential causes of each non-conforming characteristic is essential to identify the most effective and efficient rectification approach. By implementing the appropriate disposal methods, maintaining proper material control, and implementing preventive measures, manufacturers can minimize the occurrence of non-conforming lube oil blends and ensure the consistent production of high-quality lubricants.