Lube Oil Blending: A Deep Dive into Methods and Equipment
The world of lubricating oils is a complex one, where a blend of base oils and additives work together to ensure the smooth and efficient operation of machinery. But how exactly do these different components come together to create the specific oil needed for a particular application? The answer lies in the fascinating process of lube oil blending, and this article delves deep into the methods and equipment involved.
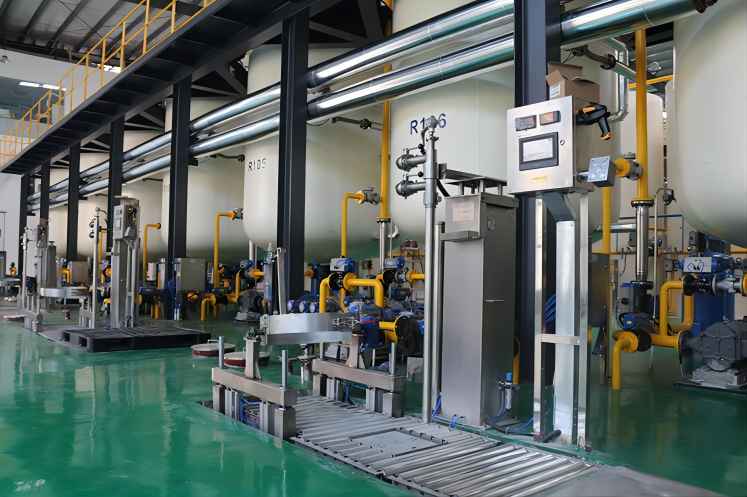
Understanding the Blend: Reconciliation Methods
Lube oil blending is anything but a haphazard toss-up. It’s a meticulous choreography of diverse methods, each playing a specific role in achieving a uniform and effective lubricant blend. Let’s unlock the secrets of these techniques and their strengths and limitations:
- Mechanical Stirring and Blending: This timeless method relies on the might of agitators, powerful rotating blades that churn the oil within the tank, creating a swirling vortex. Imagine a miniature whirlpool, pulling liquids from the depths and flinging them upwards, ensuring intimate contact and thorough mixing. This versatile technique shines in blending additives, base oils, and even defoaming agents, making it a reliable workhorse for diverse blending needs.
- Pump Circulation Blending: This method embraces the power of the cycle. A dedicated pump continuously scoops oil from the tank’s bottom and propels it back in through a strategically placed nozzle or jet agitator. The resulting jet stream acts as a potent stirrer, creating powerful currents that thoroughly homogenize the various components. This dynamic approach is particularly adept at blending base oils and additives, especially for large-scale production.
- Compressed Air Blending: This method harnesses the energy of air. Compressed air streams are injected directly into the tank, acting as invisible agitators that bubble and churn the oil. While this technique boasts efficiency for large volumes and average quality requirements, it’s important to tread carefully. The pressurized air can contribute to oil oxidation, making it unsuitable for lubricants prone to foaming or containing powdered additives. Think of it as a powerful tool, but one demanding cautious application.
- Pipeline Online Blending: This method embraces the future of precision. Imagine a real-time symphony of controlled flows. Individual streams of base oils and additives, precisely metered and monitored by automated control systems, converge in a specially designed mixer. The meticulous choreography guarantees a perfectly homogeneous blend, eliminating the need for bulky tanks and lengthy mixing times. This cutting-edge approach offers optimal control and efficiency, making it the crown jewel of modern blending techniques.
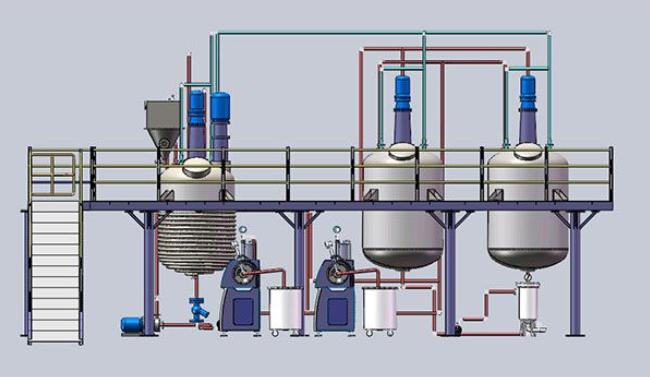
Choosing the Right Tool: The Lubricant Oil Blending Plant
Selecting the right equipment for lube oil blending is akin to equipping a master chef with the perfect utensils. Each tool has its own specialty, and choosing the ideal combination ensures a masterful blend. Let’s delve into the toolbox of essential blending equipment:
1. Mixers: The Masters of Mayhem
- Propeller Mixers: These whirling blades, like miniature helicopter rotors, are the go-to heroes for low-viscosity fluids. They create a swirling vortex, drawing liquids from the depths and flinging them outwards, ensuring fast and efficient mixing. Imagine a miniature hurricane, churning the oil into a homogenous blend.
- Paddle Mixers: These gentle giants, with their broad blades, are the slow and steady warriors of the blending world. They gently push and fold the oil, perfect for blending additives and ensuring thorough integration without excessive shear. Think of them as wise elders, guiding the components into a harmonious union.
- Turbine Agitators: These high-speed champions, with their angled blades, are the ultimate blenders for large volumes and high viscosities. They create powerful radial currents, tearing through the oil like miniature tornadoes, ensuring rapid and complete mixing. Imagine them as the berserkers of the battlefield, leaving no corner untouched.
- Anchor Mixers: These stationary sentinels, with their long, vertical blades, are the masters of scraping and agitation. They hug the tank walls, scooping up stubborn sediments and ensuring no oil is left behind. Think of them as the tireless scouts, patrolling the depths and ensuring complete integration.
2. Nozzles: The Precision Sniper
- Single-Head Nozzles: These lone wolves, strategically positioned at the tank bottom, are the sharpshooters of the blending world. Their focused jets pierce the oil, creating localized turbulence and promoting mixing. Imagine them as skilled assassins, striking key points to disrupt the oil’s stillness.
- Multi-Head Nozzles: These multi-pronged attackers, with their array of jets, are the blanket bombers of the blending battlefield. They cover the entire tank surface, creating a barrage of turbulence that ensures thorough mixing across the entire volume. Think of them as a squadron of fighters, leaving no corner untouched.
- Rotating Nozzles: These dancing dervishes, with their constantly moving jets, are the ultimate masters of chaos. They weave through the oil, creating a dynamic web of turbulence that guarantees complete and even mixing. Imagine them as whirling dervishes, leaving the oil in a state of controlled frenzy.
3. Beyond the Basics: The Special Forces
- Jet Mixers: These internal tornadoes, placed within the tank’s piping, are the ambush predators of the blending world. They create powerful suction and expulsion, drawing oil from one section and propelling it into another, ensuring rapid and efficient mixing throughout the entire system.
- Static Mixers: These silent assassins, with their intricate baffles and channels, are the masters of stealthy mixing. As the oil flows through its maze-like structure, it is constantly redirected and folded, ensuring complete homogenization without the need for moving parts.
- Homogenizers: These high-pressure warriors, with their microscopic jets, are the ultimate warriors against particle size. They break down large droplets and agglomerates into minuscule particles, ensuring a smooth, homogenous blend free of any unwanted texture.
- Evaporators: These masters of volatile removal, with their controlled heat and vacuum, are the unsung heroes of the blending world. They remove unwanted volatile components from the oil, ensuring optimal performance and stability.
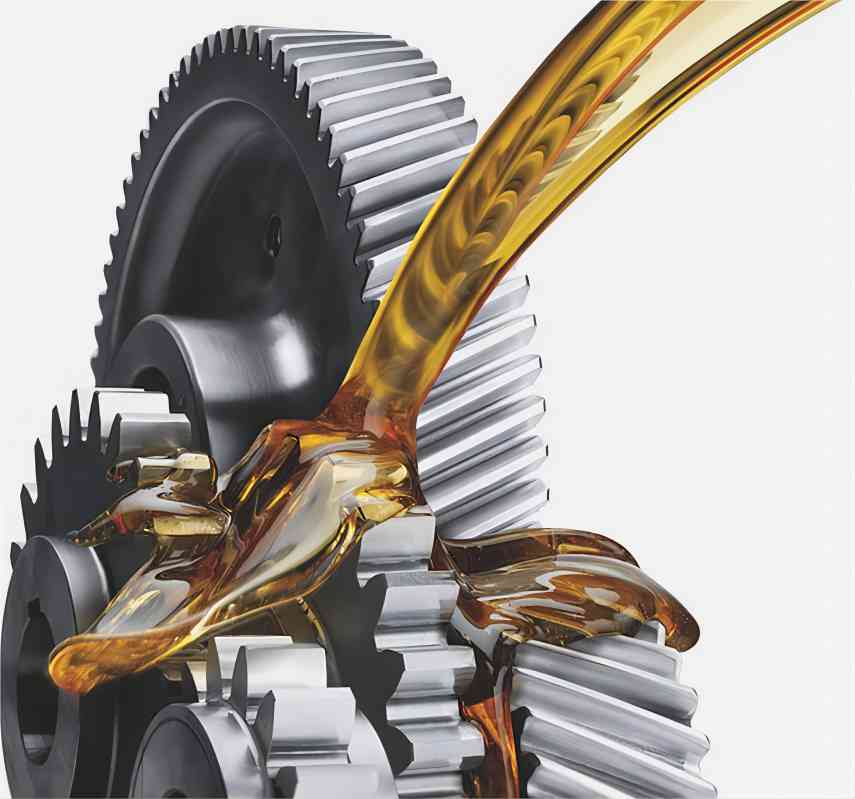
Conclusion: Blending for Success
Lubricant oil blending is an intricate dance of methods and equipment, each contributing to the creation of high-quality products. Choosing the right approach depends on factors like the desired oil properties, production scale, and budget. By understanding the available techniques and tools, lubricant manufacturers can ensure that their blends deliver optimal performance and meet the demands of a diverse market.